5 Key Differences Between Compounded and Pigmented Tank Colors
Poly Processing customers choose to color their polyethylene chemical storage tanks for a number of reasons. Tanks may be colored for aesthetics, branding, chemical identification, or to reduce transmission of radiant heat through the plastic.
There are three ways to change the color of polyethylene tanks:
- Inserting color pigments directly into the mold with raw resin
- Using a compounded resin that’s produced in a controlled environment by a resin manufacturer or resin producer
- Painting the exterior of the chemical storage tank
Let’s take a closer look at the advantages and disadvantages of each option for coloring polyethylene chemical tanks.
Adding a Color Pigment to Polyethylene Resin
Coloring a polyethylene tank by adding a pigment into a virgin polyethylene resin can cause unintended negative results. Color pigments can be contaminants at some level and often require heavy metals to discolor resin past its natural color. Pigment also affects other compounds in resin, such as UV inhibitors or antioxidants. Therefore, any time you add a pigment post-production to a polyethylene resin you possibly compromise the overall performance of the end product.
Also, different colors affect the processing of polyethylene tanks. For example, certain colors will absorb more heat or reflect more heat in the manufacturing process. Without a way to properly measure the internal temperature of the cooking cycle, you could potentially alter the manufacturing temperature significantly. Overcooking or undercooking becomes a distinct possibility. This can affect the tank’s performance by increasing the brittleness of the plastic as well as how the plastic responds to environmental factors.
Coloring a Tank with Compounded Resins
Another option for coloring polyethylene plastic tanks is by using a compounded colored resin. Compounded polyethylene resins arrive colored, directly from a supplier, with the pigment introduced in an earlier phase. This helps prevent compromising the structure of the polyethylene.
Poly Processing only uses compounded colored resins to color polyethylene tanks, because they preserve the reaction and don't affect the catalyst, or peroxide, that allows for cross-linking in XLPE tanks.
This approach gives you a more consistent and more vibrant color for your tank — no swirls or light spots where the pigment didn’t get blended enough.
Painting a Chemical Storage Tank
Another option for adding color to a polyethylene tank is by painting the exterior. Painted tanks have an advantage in that the exterior paint 100% blocks the UV. A latex paint is recommended and will prevent UV from degrading the polymer over time. This may be a good option for outside tanks storing chemicals that are highly sensitive to UV and heat, like sodium hypochlorite.
Tanks will need to be painted onsite at your facility, because scratching and scraping can occur during delivery.
Check out our tank painting guide to learn how to paint your polyethylene tank.
What Tank Color Should You Choose?
Standard tank colors tend to be black or white, but you can order a custom tank color if you like. Most of our customers who want colored tanks have a functional reason for coloring their storage tanks, although some have aesthetic reasons.
Let’s take a look at the various tank colors you can choose from.
Black Chemical Storage Tanks
Polyethylene has the positive trait of being a poor conductor of heat. Therefore, with large polyethylene tanks, such as tanks over 6,000 gallons, it will take a lot of energy to raise the temperature of the chemical just from exposure to UV. Since heat is not a big issue in this case, a black tank might make the most sense to block UV rays.
UV light and heat can degrade your tank as well as the chemical, but black resin reflects the sun and won’t break down easily under UV exposure. In fact, black resin is the best UV inhibitor available. In Poly Processing tanks, UV inhibitors are built into all of our polyethylene, but the black resin extends the life of the tank outdoors.
Some customers are concerned about how much a black tank will heat up under a full day of direct sun exposure. While all black materials heat up under the sun more than light-colored materials do, polyethylene is a poor conductor of heat. In large tanks, it takes a lot of energy to raise the temperature of the chemical simply because of UV exposure.
In most cases, the tank wall is thick enough that the sun will begin to set before the heat reaches the chemical in the tank.
White Chemical Tanks
With small tanks or in warmer environments where ambient temperature is high, a few degrees difference may create off-gassing issues with temperature sensitive chemicals. In that case, a white or lighter colored compounded resin polyethylene tank would make most sense to deflect heat.
With a high ambient temperature and UV exposure, painting a tank, or insulating and painting the insulation would likely be the best solution. The insulation provides temperature stability while the mastic paint coating blocks all UV exposure to the polyethylene tank.
Other Colors for Your Chemical Storage Tank
Sometimes you don’t have a functional need for a black or white tank, but you have an aesthetic need to add color to your chemical storage tank. Some of our customers want their tanks to match their brand colors, to blend in with the landscape, or to match the outside of their building.
Poly Processing can match many colors. If you’re ordering a colored resin tank, the supplier requires a minimum order of resin in most cases. This may make the compounded resin choice unavailable. Alternatively, you can paint the tank on-site.
For questions about coloring polyethylene tanks or to determine what color you should choose for your specific tank application, contact a chemical storage tank expert.
- April 10, 2023
- Topics: Fittings and Accessories
About Poly Processing
Posts By Topic
Tech Talk Podcast Episodes
Subscribe By Email
Recent Posts
- Lids for Fume-Tight Tanks: What Are My Options?
- Insulating Your Chemical Storage Tank: Why It Matters and How to Do It
- Essential Fittings and Accessories for Chemical Storage Tanks
- Choosing the Right Secondary Containment System: An In-Depth Evaluation of Your Options for Safe Storage
- The Inner Workings of Chemical Storage Tank Venting Systems
Tank Configurator
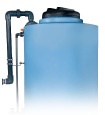
Find the recommended tank and system components for your chemical storage challenge.
Configure a Tank Package