A Brief Introduction to Poly Processing’s Rotational Molding Process
From pink yard flamingos to dump truck beds, and hundreds of other sized products in between, rotational molding is an efficient manufacturing process. Rotational molding is especially effective in the manufacturing of chemical storage tanks. Let’s look at the advantages of rotational molding, and the value Poly Processing can bring to you.
Rotational molding involves a heated hollow mold which is filled with a charge or shot weight of material. It is then slowly rotated (usually around two perpendicular axes) causing the softened material to disperse and stick to the walls of the mold. In order to maintain even thickness throughout the part, the mold continues to rotate at all times during the heating phase and to avoid sagging or deformation also during the cooling phase. The process was applied to plastics in the 1940s but in the early years was little used because it was a slow process restricted to a small number of plastics. Over the past two decades, improvements in process control and developments with plastic powders have resulted in a significant increase in usage.
Rotational molding: Advantages for Chemical Storage Tanks
Storage tanks are rotationally molded using high density cross linked polyethylene. Using the rotational molding process, the tanks are a one-piece, monolithic, seamless vessel. Unlike steel tanks, weld seams are eliminated. A 6500 gallon steel tank can contain up to 70 yards of welded seams, or 70 yards where chemicals can potentially leak.
As opposed to fiberglass tanks, rotationally molded tanks are a homogenous, one-layer construction. This one layer construction eliminates potential weak spots in the tank structure and eliminates wicking or delamination due to chemical attack or poor construction.
Thickness of the tank with rotational molding is maximized at the tank sidewalls and bottom knuckle radius. This creates extra strength where it’s needed. The lower sidewalls and bottom knuckle radius are engineered to handle the hoop stress that is placed on the tank due to the chemical being stored.
Click below to watch a short video of rotational molding in action.
Poly Processing Rotational Molding Capacity:
Poly Processing manufactures rotationally molded vessels in three locations located across the United States. Monroe, Louisiana. French Camp, California. Winchester, Virginia. The nine rotational molding machines can manufacture vessels from 30 gallons up to 14,000 gallons and tanks as large as 14 feet in diameter by 18 feet tall. Custom sizes and shapes to fit your unique storage requirements are available as well.
For additional information on rotational molding or to discuss manufacturing a custom tank, please contact a chemical storage tank expert.
- November 19, 2013
- Topics: Value Added
About Poly Processing
Posts By Topic
Tech Talk Podcast Episodes
Subscribe By Email
Recent Posts
Tank Configurator
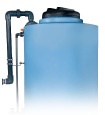
Find the recommended tank and system components for your chemical storage challenge.
Configure a Tank Package