Easy Level Monitoring with the Reverse Float Level Gauge [VIDEO]
You need to know how much chemical is in your storage tank so you can order more product at the right time to continue business without missing a beat. Not only that, but certain chemicals have to be stored at specific levels to maintain their properties. Replacing the chemical too early or too late can stall your operations, ruin your inventory, and impact your profits.
The Poly Processing Reverse Float Level Gauge makes it easy to monitor the levels in your chemical storage tanks. Unlike many other tank level indicator gauges, the reverse float level gauge is a simple system that doesn’t require channeling the chemical to the outside of the tank in order to see the level. The gauge is installed on the outside of the system for easy monitoring, but the chemical stays inside the tank. If the gauge pipe cracks or breaks, there’s no danger of the chemical siphoning out of the tank.
Watch this quick video to see how the reverse float level gauge works.
Why Use a Reverse Level Gauge?
A level gauge monitors the liquid level of the chemical in the polyethylene tank. There are several types of gauges, and Poly Processing works with many types of level indicators, including clear tube level gauges and ultrasonic level gauges. But in almost all cases, we recommend our reverse float gauge for its simplicity and ease of maintenance.
How the Reverse Float Level Gauge Works
Poly Processing’s reverse float level gauge consists of a float inside the tank, which bobs on the surface of the chemical. The float is compatible with any kind of chemical that can be stored in a Poly Processing tank. The float is attached to a rope, which travels through a clear vertical pipe on the outside of the tank. A level indicator is attached to the end of the rope.
As the tank is filled, the chemical lifts the float inside the storage tank, and the level indicator on the outside is lowered. As a reverse gauge, the level indicator shows the reverse of a tank’s level—the lower the indicator, the fuller the tank.
The reverse level gauge uses a pulley system with polypropylene rope, nylon rollers inside of PVC elbows, clear pipe, and a level indicator. The external components are dry-fit together, not glued. Assembling and replacing the gauge is easy and only takes a few minutes. Maintenance is simple, and individual pieces can be replaced, if needed.
Benefits of the Reverse Float Level Gauge
While the level indicator isn’t intended for precise monitoring or metering, it reliably provides a basic, easy to read indication of your chemical storage tank’s capacity. The gauge is ideal for facilities that need to know when to refill their tanks, but don’t need precise volume numbers.
The reverse float level gauge provides additional benefits, including:
- No stains on the clear pipe from chemicals or UV attack
- No siphoning of the tank if the pipe breaks, because there is no chemical in the external pipe
- The internal float is designed to work with 1.0 to 1.8 specific gravity fluids
- No chemical burns or chemical spurts on operators
- Reverse calibration tape can be added for tank capacity
- Provides mechanical verification of ultrasonic or other electronic level sensor
The reverse float level system can be used on almost any tank, including double-walled SAFE-Tanks. There are different dome mounted fittings used for the reverse float gauge. If the fitting is installed on the flat you can use a PVC or SS bulkhead fitting. On the curvature of the dome you must use the universal ball dome fitting or made vertical curved fitting.
Download the Reverse Float Level Gauge guide here.
Talk to a chemical storage tank expert today to learn more about the Reverse Float Level Gauge.
- September 19, 2022
About Poly Processing
Posts By Topic
Tech Talk Podcast Episodes
Subscribe By Email
Recent Posts
Tank Configurator
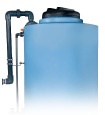
Find the recommended tank and system components for your chemical storage challenge.
Configure a Tank Package