How Chemical Stress Can Lead To Polyethylene Tank Cracks
In most polyethylene chemical storage tank operating and loading applications, a tank failure is primarily due to two types of stresses: chemical stress or mechanical stress.
Let's explore how chemical stress can cause cracks in polyethylene chemical storage tanks and advanced tank solutions that resist cracking.
What Causes Chemical Stress?
Most polyethylene chemical storage tanks are inherently robust and resist chemical forces that cause degradation and cracks because the forces of the chemical stress are dispersed over a wide area of the tank. However, external stresses over a lifetime of use can break down the tank’s properties, potentially causing cracks. If cracks occur, it’s recommended that you replace the polyethylene tank.
Chemical stress occurs when the chemical stored in the tank oxidizes or "plasticizes" the polyethylene. It's a combination of stress and degradation of the polyethylene itself. The chemical pulls electrons from the molecular chain of the polyethylene. As a result, the polyethylene molecular chain becomes susceptible to oxygen attack. Over time, as oxygen attacks the polyethylene, the tank becomes brittle and leads to stress cracks.
Plasticizing of polyethylene is not as prevalent as oxidation. A plasticizing chemical modifies the molecular structure of a polyethylene tank. As a result, the tank wall is softened, causing increased swelling and expansion. Fortunately, only a hand full of chemicals will plasticize polyethylene and are not recommended for use in a polyethylene tank. These include hydrocarbon based materials such as 2 cycle oil, gasoline, etc.
Advanced Chemical Storage Solutions
Poly Processing tanks are produced with superior crosslinked polyethylene resin and are engineered to resist chemical stress cracking. High-density crosslinked polyethylene affords a tremendous advantage over linear polyethylene and fiberglass in resisting chemical stress.
Most linear polyethylene used for tank manufacturing is rated between 250 and 600 hours of continuous exposure to harsh chemicals. Poly Processing's high-density crosslinked polyethylene is rated for a longer tank service life of over 1,000 hours of continuous exposure to harsh chemicals, thus resulting in a lower total cost over the life of the tank. Many Poly Processing tanks have withstood continuous storage of harsh chemicals for 25 years or more.
Finally, it's important to make sure you consider the chemical being stored in the tank design. For instance, sulfuric acid and sodium hypochlorite are aggressive oxidizing chemicals. Poly Processing's exclusive OR-1000™ system is specifically engineered to resist the oxidation and chemical stress caused when storing these chemicals.
In our next post, we'll examine how mechaical stress can lead to poly tank failure and what steps you can take to prevent that from happening.
For more information on designing a storage tank to resist the damages of chemical stress, please contact a chemical storage tank specialist.
- March 18, 2014
- Topics: Value Added
About Poly Processing
Posts By Topic
Tech Talk Podcast Episodes
Subscribe By Email
Recent Posts
- The Largest Crosslinked True Full Discharge Tanks Available: 15,500 IMFO and 15,000 Sloped Bottom IMFO
- Contained Bottom Discharge for Double-Wall Tank
- Join Us at WEFTEC 2025 Conference & Exhibition
- Effective Wastewater Treatment Chemical Storage
- How to Safely Store Sulfuric Acid to Overcome its Corrosive Nature
Tank Configurator
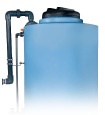
Find the recommended tank and system components for your chemical storage challenge.
Configure a Tank Package