How Hydraulic Fracturing Works
Hydraulic fracturing, also known as fracking or fracing, is the process of making small cracks or fractures in underground rocks to release the oil or natural gas inside. Scientists must analyze the physical characteristics of the rocks to be fractured before fracking can begin.
The Fracking Process
Narrow shafts, or boreholes, are drilled into the rocks and cased with steel pipes. A pressurized mixture of water, sand and chemicals, known as fracking fluid, is then injected into the rocks. The fluid cracks the rocks and fills the cracks with sand, allowing natural gas or oil to flow up the boreholes. Following fracking, wastewater, known as flowback, returns to the surface for collection. It is then stored in tanks or pits for treatment or disposal. On-site storage and treatment facilities eliminate the need to truck flowback off-site.
Mitigating Fracking Risks
Fracking fluid typically contains between three and 12 chemicals, depending in part on the characteristics of the rocks being fractured. Commonly used chemicals include hydrochloric acid, calcium chloride, sodium chloride, sodium hydroxide and citric acid. These chemicals serve various purposes, from controlling bacteria to decreasing corrosion of the steel casing. Hydraulic fracking poses a risk of surface and groundwater contamination through chemical leaks and spills onto the ground or into nearby rivers and streams. This risk can be minimized through proper chemical storage.
Smarter Chemical Storage Solutions
As a leader in cross-linked polyethylene chemical tanks, Poly Processing provides safe and reliable solutions for on-site chemical storage. Our extensive product range includes:
Vertical Tanks with Integrally Molded Flanged Outlet
Our vertical tanks with Integrally Molded Flanged Outlet (IMFO®) help minimize the risks associated with traditional vertical tank maintenance. They also offer superior long-term structural integrity and net positive suction compared to tanks with post-production inserts.
SAFE-Tank® System
Our SAFE-Tank® System is a "tank-within-a-tank" system that protects against interstitial contamination. It eliminates the need for expensive, high-maintenance secondary concrete containment areas.
PolyGard™ Steel Vessel Lining
Our PolyGard™ Steel Vessel Lining is a medium-density polyethylene lining for stainless steel and carbon steel tanks. Popular with national rental companies, it molds to the inside of a tank, acting as a barrier between the steel and the substance being stored.
With manufacturing facilities in Louisiana, California and Virginia, we can ship your order from the facility closest to you, saving both time and money.
To find out more, contact our storage tank specialists today.
- December 18, 2015
- Topics: Applications
About Poly Processing
Posts By Topic
Tech Talk Podcast Episodes
Subscribe By Email
Recent Posts
Tank Configurator
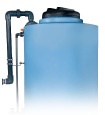
Find the recommended tank and system components for your chemical storage challenge.
Configure a Tank Package