Saving Cost and Improving Accuracy When Using Ultrasonic for Tank Level
Installing ultrasonic level systems for your tanks allows you to monitor liquid levels with added safety and less chance of contamination. These systems constantly track how much is in the tank and display the information remotely.
The Advantages of Ultrasonic Level Systems
Ultrasonic level systems have two main advantages over other products designed to monitor tank levels.
- Non-contact monitoring. Other monitoring systems require contact with the liquid for consistent measurement. This creates potential problems with contamination and more frequent maintenance requirements. Some fluids are caustic or may have chemical compatibility issues with materials used in a traditional level monitoring system. The fluid could eat away your probe, simultaneously giving you a repair bill and contaminating the remaining fluid. Ultrasonic sensors never touch the fluid in your tank, eliminating these issues.
- Electronic monitoring. With an electrical signal, you also get the benefit of remote monitoring. Someone on the ground or in a control room can look at a screen or indicator and monitor tank levels. This adds safety and convenience, saving you time and money.
How to Choose The Right Level System
Choosing the right level system often depends on the type of tank, the way it is set up and the liquid being stored. Caustic liquids or liquids that need to be stored at high temperatures may damage mechanical or contact systems. Foaming chemicals need a different type of setup from the norm such as a stilling well pipe or the use of radar technology.
Where and how you install an ultrasonic level plays an important role in how accurately it measures liquid levels.
Setting Up an Ultrasonic Transducer to Avoid Installation Issues
For the best installation of an ultrasonic transducer, you need to ensure that there is as little dead space or acoustic signal impedance as possible and that nothing interferes with the signal. Dead space or acoustic signal impedance is increased by the length of the nozzle the transducer is mounted to.
A 2” universal ball dome fitting allows you to meet the best case installation set-up because it is mounted directly to the dome of the tank, does not require special geometry to get the correct beam from the transducer, and can save the customer substantial money versus a made vertical fitting which has to be bolted to the tank and usually includes a spool piece that the transducer has to shoot through.
You can adjust the UBD fitting if necessary to make sure the system stays in calibration at all times and reduce potential bounce of the sidewalls of the tank. This is important for long term accuracy. As rigid fittings on the dome can begin to lean or tilt due to temperature swings, dome changes, etc. The locking ball system on the UBD allows for slight adjustments in angling the beam away from tank walls and maintaining calibration without the installation of expensive and needless fitting systems. This UBD normally does not need a flange so you can you reduce the length of the fitting and in turn reduce dead space while increasing accuracy of the system.
Since an ultrasonic level measures using a cone of sound, it is important that it be installed as close to the center of the tank as possible. The locking nut on the UBD loosens and re-tightens to fit snug around the measuring instrument, reducing the risk of vibration interference. A UBD can even be used interchangeably with both an ultrasonic or radar level. The UBD fitting is normally 80-90% less expensive than a rigid made vertical fitting in normal operations.
When Not to Use Ultrasonic Levels
Ultrasonic may not always be the best level detection choice, nor the only choice. While ultrasonic levels work well in many settings, there are times when you might need to go with a radar or reverse float gauge or a combination of both systems. Ultrasonic levels do not read well through dense moisture or heavy vapor. Anything that affects sound travel in the air will affect your readings with an ultrasonic system. Many customers prefer to have mechanical level system as well as an ultrasonic or radar system. This allows for redundancy and gives the operator a double check system against the electronic readout to make sure it is working correctly.
Poly Processing has developed the reverse float gauge. The reverse float level gauge is unique in that it is a simple mechanical system which does not require chemical on the outside of the tank to give the user a reading. The reverse float level system can be used on almost any tank including double walled SAFE-Tanks. This system gives the end user simple redundancy. The reverse float level gauge does not require any sidewall penetrations, will not allow siphoning of the tank if the pipe breaks, and keeps the operators safe as there is no chemical in the external portion of the system.
Poly Processing has trained staff to answer any questions you might have regarding the best level system for your particular use. We can help find the safe and most effective monitoring system for your tank.
To learn more about our chemical storage solutions, reach out to one of our experts today.
- January 21, 2016
- Topics: Fittings and Accessories
About Poly Processing
Posts By Topic
Tech Talk Podcast Episodes
Subscribe By Email
Recent Posts
Tank Configurator
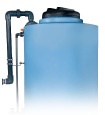
Find the recommended tank and system components for your chemical storage challenge.
Configure a Tank Package