Is Your Polyethylene Chemical Tank Built For the Right Temperatures?
Poly Processing’s standard crosslinked polyethylene tank systems can withstand process temperatures up to 100°F — but that figure can be misleading, because there are different types of temperature to consider.
For example, one of our customers in Texas asked about keeping a polyethylene tank outdoors in extreme temperatures:
I am concerned about using a 4400-gallon SAFE-Tank for storage of concentrated sulfuric acid outside…I looked around your website and found the 100°F limit. Lately in summer we have been 105°F to 110°F, and this tank is in direct sun in the afternoon.
If your company is in a region that gets extremely hot, this could be a concern for you as well. How worried do you need to be about exposing your chemical storage tank to heat or cold, and what should you do about it?
When it comes to temperature, there are two concepts to understand: ambient temperature and process temperature. When we talk about the highest temperature a tank can take, it’s important to understand both aspects.
Ambient Temperature vs. Process Temperature in Chemical Storage
Ambient temperature is the external air temperature — the outdoor temperature, or the air temperature of your facility (if storing indoors). Ambient temperature has very little effect on the tank or the chemical content in the tank, because ambient temperatures fluctuate too quickly.
First, the heat needs to penetrate the plastic tank, then it needs to heat up hundreds or thousands of gallons of chemicals. This takes more than just a few hours. Even in the hottest areas of the country, by the time the environmental temperature begins to warm the chemical, the sun is already descending and the ambient temperature is falling. Thus the chemical’s temperature changes very little due to ambient temperature fluctuations.
Process temperature relates to the temperature of the content or chemical in the tank. When the temperature of the chemical itself elevates, that’s a process temperature change. Process temperature affects the tank much more than ambient temperature does. As a result, process temperature, or chemical temperature, has a major role in determining tank thickness (along with chemical concentration, weight, and oxidation). This is the temperature limit that we refer to on our website.
Some chemicals must be stored at specific temperatures because of their chemical properties. Once a chemical like sodium hydroxide falls below a certain temperature, it will crystalize or freeze.
Temperatures Can Fluctuate
Process temperature can fluctuate, depending on how you’re handling your stored chemicals. Usually, this is related to delivery or mixing. Some chemicals, like alum, ferric and polymer, are delivered at higher temperatures, and they cool while being stored. Others are mixed during storage, creating a reaction that raises the chemical’s temperature.
For example, some chemicals are delivered in bulk at a higher concentration, to reduce costs. At delivery, they need to be diluted with water. If it’s a chemical like sodium hydroxide, dilution can cause an exothermic chemical reaction, which elevates the process temperature within the tank.
Poly Processing can help you design the right storage system for your specific application.
How Heat Impacts Your Polyethylene Tank
It’s possible to purchase a standard polyethylene storage tank that meets general ASTM specifications, which is prepped for a maximum of 73 degrees. However, by using a tank that merely meets ASTM standards, a chemical temperature above 73.4 downgrades the maximum allowable hoop stress. This results in a compromised tank that can fail unexpectedly.
At Poly Processing, the design hoop stress for a 100°F service temperature is applied as a maximum hoop stress and is derated for service temperatures above 100°F using a constant service factor of 0.475. So your tank may be built thicker, based on the calculation of chemical heat and specific gravity. Download our ASTM D-1998 Technical Training Document here.
It’s important to have an upfront understanding of the temperatures your tank will be exposed to — even for short periods. Cross-linked polyethylene (XLPE) chemical storage tanks and polyethylene tanks in general expand and contract as chemical and environmental temperatures fluctuate. The tanks must be designed with consideration for the chemical and the temperature that the chemical will be stored at.
If a warmer chemical is stored or delivered in a tank not designed for those metrics, the tank can expand until it exceeds allowable hoop stress. On the other hand, a tank that is properly designed and manufactured to meet the particular needs of your chemical and application will perform reliably for many years.
For more information on elevated temperatures and storage tanks, contact one of our chemical storage tank experts.
- February 10, 2025
- Topics: Value Added
About Poly Processing
Posts By Topic
Tech Talk Podcast Episodes
Subscribe By Email
Recent Posts
- The Complete Journey of Owning and Retiring a Polyethylene Storage Tank
- Is Polyethylene a Storage Solution for Elevated Temperature Tanks?
- The Economics of Chemical Storage: How to Maximize ROI on Your Tank Investment
- Lids for Fume-Tight Tanks: What Are My Options?
- Insulating Your Chemical Storage Tank: Why It Matters and How to Do It
Tank Configurator
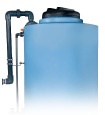
Find the recommended tank and system components for your chemical storage challenge.
Configure a Tank Package