A Closer Look At the Toughness of XLPE Through Testing
We get a lot of questions about the standard testing on chemical storage tanks that we do at our facility. Vertical tanks larger than 500 gallons in most cases are extensively tested to ensure that they meet ASTM standards. Depending on customers’ needs, we also offer additional testing on our chemical storage tank systems.
Let's take a look at the types of chemical tank testing that Poly Processing performs, how we do it, and why these tests are so important in the chemical storage tank production process.
Four Main Types of Testing
At Poly Processing, in most cases, we perform standard testing or verification on all vertical, IMFO®, and SAFE-Tanks® over 500 gallons, per ASTM guidelines. There are four main standard tests.
ASTM Gel Test
According to the ASTM standard D 1998-21, at least 60 percent of a cross-linked polyethylene (XLPE) tank sample must consist of cross-linked molecules to be classified as XLPE.
To perform the gel test, we take a small sample from the innermost 1/8” of the tank wall, measure it on a gram scale, and submerge it in boiling Xylene for 16 hours. The Xylene dissolves the linear polyethylene from the sample, leaving only cross-linked resin material. The sample is dried, remeasured, and compared to the original mass. The difference indicates the percentage of cross-linked polyethylene in the tank material.
ASTM Impact Test
The impact test determines the chemical tank's structural integrity through impact, rather than a chemical process. The goal is to verify that the material can withstand mechanical stress and other challenges associated with long-term chemical storage.
During the impact test, an XLPE sample is frozen overnight at -20 degrees F. It is then placed in a machine where a 20-pound “dart” is dropped at a certain foot-pound to create the appropriate impact. There are different calculations for the required impact. The thicker the tank material, the higher the impact.
The impact test produces a value that indicates the quality of the chemical tank. A tank meeting ASTM D1998 Standards will provide greater longevity and resistance to higher mechanical stress.
Hydrostatic Test
The hydrostatic test verifies that the storage tank and its fittings are leak proof. This one-hour test is performed on most tanks 500 gallons and above, and any tank with fittings installed.
ASTM standards require that the tank sits for 30 minutes to verify that there are no leaks. At Poly Processing, our internal standard is to test for one hour, so that we can verify that the fittings and the tank itself can withstand hydrostatic pressure.
Ultrasonic Test
The ultrasonic test verifies a consistent wall thickness, within upper and lower parameters, of a chemical storage tank. To make sure the tank meets ASTM standards, w use a sonar instrument to verify the thickness of the walls at various points around the diameter and vertically along the tank sidewall.
Standard wall thickness readings are taken at 0 degrees, 90 degrees, 180 degrees, and 270 degrees at 1-foot, 2-foot, and 3-foot elevations.
The Poly Processing Tank Drop Test
One other test that only Poly Processing has passed is the Tank Drop Test, which we have recorded for our customers.
In the Tank Drop Test, three drops were performed, using 3,000-gallon tanks. The first test consisted of two chemical tanks, one made from crosslinked high-density polyethylene and the other from linear polyethylene. The rotomolded tanks were fabricated in accordance with the instructions and guidelines highlighted in ASTM D1998. This ensured that these tanks met the quality requirements of optimum cure and proper fabrication.
In each test, the tanks were filled with water and dropped onto a concrete surface from a crane.
The First Drop
Each tank in the first set was filled with 7,000 pounds of water and lifted by crane 15 feet in the air. The tank was released to free-fall onto a concrete surface below. While the linear tank catastrophically failed, the crosslinked polyethylene tank didn’t fail or develop any cracks.
If you look closely at the linear polyethylene tank, you can see that the impact created a crack that quickly unzipped as the tank finished impacting the ground. This unzipping is a characteristic found in linear polyethylene resin grades.
The Second Drop
After the first drop, we filled the exact same Poly Processing crosslinked tank with 11,000 pounds of water (more than 15 times the weight of an empty chemical tank). The tank was dropped from the same height, to the same surface with no damage to the tank.
The Third Drop
Finally, the same tank was dropped from the full height of the crane — 45 feet in the air — onto the concrete surface. Even after the third drop, containing 11,000 pounds of water, the tank remained 100 percent intact with no leaks or cracks.
The Toughest Chemical Tanks in the Industry
These tests are an impressive demonstration of our XLPE tanks’ durability and strength, but they’re more than just for show. The strength and longevity of our chemical storage tanks are our top priorities. We’re committed to manufacturing the most robust chemical storage tanks in the industry — so we’re always working to improve the durability and useful life of our XLPE tank solutions.
Dramatic testing like the drop test allows us to put our tanks through the most extreme conditions so that we can guarantee their quality to our customers. Your employees’ safety and your company’s operations depend upon it.
Want to see more tank tests? You can view other Poly Processing quality tests on our YouTube channel.
For more information on the testing we do, contact a chemical storage tank expert at Poly Processing today.
- August 26, 2024
- Topics: Tank Design and Materials
About Poly Processing
Posts By Topic
Tech Talk Podcast Episodes
Subscribe By Email
Recent Posts
Tank Configurator
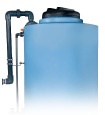
Find the recommended tank and system components for your chemical storage challenge.
Configure a Tank Package