What Is the Best Chemical Storage Solution for Paper Mills?
Paper mills use harsh chemicals on a daily basis in the production of pulp and paper. These chemicals can be hazardous to the environment and to workers’ health, so it’s critical to install a chemical storage system you can rely on.
Let’s take a look at the chemical needs of paper mills, their storage requirements, and some recommendations for systems that meet or exceed your performance needs.
The Pulp and Papermaking Process
The process of making paper involves turning wood into pulp, then into a slurry that becomes paper. The procedure involves harsh chemicals at various steps.
- Preparing the raw material. Depending on the pulping process and the raw material, wood is debarked and chipped. Chips are screened for size, cleaned, and set aside for further processing.
- Separating the fiber. Fibers are separated from the chips in a process that involves pressure cooking in chemicals and steam treatment. Some methods involve stone grinding rather than chemical treatments.
- Bleaching Process. To produce a white paper, the raw pulp usually undergoes a bleaching process. This may involve chlorine dioxide, chlorine gas, sodium hypochlorite, hydrogen peroxide, and oxygen.
- Papermaking. Pulp and water are mixed together to form a pulp slurry that normally contains less than one percent fiber. The slurry is screened in centrifugal screens and is sent through a paper-forming machine, where the fiber slurry is uniformly spread and a paper sheet is formed.
The papermaking process relies on harsh chemicals that can harm the environment and injure personnel. Proper chemical storage at a paper mill doesn’t simply protect inventory — it protects your most valuable assets.
Chemical Storage Requirements for Making Paper
Paper companies require a chemical containment system that can reliably and safely store harsh chemicals without fear of a tank failure. Not every chemical storage tank is created equal, and it’s vital to understand the differences between various types of systems.
Poly Processing supplies several paper mills throughout the country with chemical storage tanks for many papermaking chemicals, including:
- Coating binders — added to increase water retention on the paper’s surface, making paper more durable. One of the most commonly used chemicals is dextrin.
- Bleaching chemicals — used to whiten paper. Chemicals used include hydrogen peroxide, sodium hypochlorite, and chlorine dioxide.
- Retention agent — used to treat filler material that sometimes bind to the fibers. One of the most commonly used retention agents is calcium carbonate.
- Caustic soda — used to increase the pH of the pulping mix for smoother fibers.
Other papermaking chemicals that Poly Processing stores in our tanks include:
- Alum - For alkaline sizing
- Soap - De-inking
- Sodium bisulfite- Neutralization
- Sodium Aluminate - Ph control
- Sodium Bisulfite - Used in pulping
- Sodium Silicate - Ink dispersion, peroxide stabilization
Reliable Storage Solutions for the Papermaking Industry
Poly Processing’s cross-linked polyethylene chemical tanks are an ideal solution for storing papermaking materials. Let’s take a look at three of three of the innovative storage solutions our customers are using.
SAFE-Tank®
The SAFE-Tank is a double-wall plastic storage tank that provides a “tank-within-a-tank” to safely store chemicals. The system prevents damage and injury from chemical exposure without the need of an additional containment unit. Not only does this save space in your facilities, but it makes it easy to relocate your storage tanks if the need arises.
The SAFE-Tank provides a minimum of 110% secondary containment by enclosing the primary storage tank within a sealed outer tank. If the primary tank develops a leak, the escaping liquid is safely contained in the interstitial space between the primary and outer tanks. Because the space is sealed, no contaminants can enter.
Because the leaked chemical is still 100-percent contained, you can continue using the chemical in your daily operations. There’s no cleanup of hazardous liquids, no loss of inventory, and no stoppage in production.
IMFO® Tank
Traditional tank maintenance can be a challenge with many chemicals – so Poly Processing engineered an innovative system that minimizes the hazards of traditional vertical tank maintenance.
Our Integrally Molded Flanged Outlet® (IMFO) System features a flange that is molded while the tank is manufactured. The flange is one piece with the tank, making it a stress-free component and eliminating the risk of stress-related leaks.
Unlike other tanks, the flange is located at the very bottom of the side wall, below the knuckle radius of the tank. This allows the tank to drain completely, in most cases without manual cleanout.
Sloped-Bottom IMFO® Tank
We also recommend the Sloped-Bottom IMFO Tank. Like the IMFO Tank, this solution offers an integrated flange below the knuckle radius. In addition, the floor of the tank is sloped towards the IMFO, giving you the greatest possible full-drain system in a vertical tank design. The Sloped-Bottom IMFO allows even heavier materials such as sludge, FOG, and thicker chemicals to discharge completely.
Have questions about polyethylene storage tanks for the papermaking industry? Contact a chemical storage tank specialist today.
- July 13, 2020
- Topics: Chemicals, Chemical Storage
About Poly Processing
Posts By Topic
Tech Talk Podcast Episodes
Subscribe By Email
Recent Posts
Tank Configurator
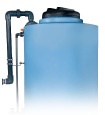
Find the recommended tank and system components for your chemical storage challenge.
Configure a Tank Package