Considerations When Choosing Tank & Pump Combinations
We’re all well versed on how important it is to choose your chemical storage tank based on the specific chemical you’re storing. The same goes for the pump you choose. Just as there are different tank options better for one chemical or another, certain chemicals and the location of pump require pump design and selection by an expert. Your Poly Processing distributor has carefully been chosen to be a systems expert, capable of combining features of the tank with other fluid handling equipment such as the pump.
Let’s examine a few of the basics, however, in order to choose the proper polyethylene chemical storage tank and pump combination.
Tanks & Pumps Based on Chemical Characteristics
To determine the type of pump/tank combination you need, first consider the fluid and process characteristics of the chemical. A good place to start would be to know the answers to some important questions. These will be useful data points to collect for your Poly Processing distributor.
- Does the fluid easily vortex?
- Is it batch sensitive?
- Is it a foaming chemical?
- Where will the pump be located relative to the tank? (distance and height)
- Does the fluid change between batches? Are batches contamination-sensitive?
- Are tanks subject to clean-up between batches?
- Will precipitates form and settle in tank? Will outlet pass them to pump?
You have to ask all of these questions before you decide what pump and tank combination you need.
A viscous fluid can benefit from a progressing cavity pump or gear pump that will draw from a cone-bottom tank or IMFO tank to get adequate feed into the pump suction. The IMFO provides less velocity to the suction port of a pump but more so than a typical fitting. The IMFO is often sufficient, however, and less costly than a cone bottom because no metal work frame is required for the tank. The IMFO has angled sloped bottom options as well. A second advantage of the IMFO is that the pump can more easily be placed away from the tank without much drag on the suction supply, whereas the cone bottom usually has the pump directly under the tank and more difficult access for maintenance and safety. So for viscous fluids consider IMFO, then sloped bottom IMFO, then cone bottom - depending on needed velocity of fluid viscosity to the pump suction head.
Water and other "water like" chemicals, however, can also bring in centrifugal, double diaphragm or air-operated pumps for transfer needs such as Bulk tank to Day tank. A diaphragm or peristaltic pump (hose pump) will often be used for chemicals that need to be metered into a pipe stream for accurate dosing requirements. The properties of the chemical dictate the type of pump materials and, conversely, the type of tank. Polyethylene (PE) is very compatible with most chemicals and what your tank wall is made of. When available seek these materials for the chemical pump as well. Another materials check can be that elastomers and alloys on tank fittings and the pump materials match.
In chemicals that require batch processing, you can chose a cone-bottom tank or you can choose a vertical chemical storage tank with an integrally molded flanged outlet (IMFO) drain that presents certain advantages to batch processing, such as:
- Fully drainable
- Fully cleanable between batches
- Compliant for FDA or NSF applications that require a CIP process
The full drain allows a complete rinse from simply hosing from the manway. This prevents any need for Confined Space Permit Entry and still achieve a clean tank in minimal time for a new batch mix.
Cone bottom tanks minimize vortexing, and are also able to handle chemicals with some solids present, though a vertical tank with a full-drain feature might be even better for that application; it is also recommended for fluids subject to separation. The tank, fitting, plus a mixer, can blend and totally drain the fluid out of the tank. It is important to note whether the tank can eliminate both vortexing and precipitate or make your pump designer aware that these conditions will exist.
Concerns Between the Pump and the Tank
The tank, pump, fittings and connectors all make up a tank system that has to effectively store and pump your fluids, all the while minimizing danger and exposure to chemicals. Since the right tank configuration can also reduce the amount of chemical you wind up wasting and save manpower and resources, it’s important to consider the tank and pump when choosing fittings and plumbing.
For instance, polyethylene tanks move, so they need a pump feed with a flexible joint to minimize the stress associated with the movement produced by filling and pumping a tank. The flex is also important to protect the tank from pump vibrations, especially from AOD pumps. Lastly a valve should isolate the tank from both the flex and the pump, so maintenance or integrity checks can be performed on either.
Pumps can also be used for mixing. In such cases a fitting will be installed both high and low on the tank, often the sidewall. In such cases leak proof protection from such movement should be a high priority. For the bottom sidewall fitting in this instance, a BOSS fitting is the most reliable fitting on the market today.
Whatever the fluid and pump required, Poly Processing’s 40 years of experience have given us the knowledge to help you find the right tank and accessories needed to ensure a safe and effective chemical tank storage system.
- March 31, 2015
- Topics: Fittings and Accessories
About Poly Processing
Posts By Topic
Tech Talk Podcast Episodes
Subscribe By Email
Recent Posts
Tank Configurator
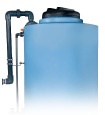
Find the recommended tank and system components for your chemical storage challenge.
Configure a Tank Package