Quality Assurance Process for Polyethylene Chemical Tanks
Poly Processing has three manufacturing plants in the United States. In each facility, we use a multi-step quality control process that meets and/or exceeds industry standards, including ASTM D-1998. The ASTM D-1998 standard is designed to give end users a margin of safety and peace of mind. It’s a voluntary standard, and not all tank manufacturers follow it.
Some tank manufacturers, including polyethylene, stainless steel, and fiberglass (or FRP), rely solely on ISO certification or other general standards. ISO regulates the consistency of a procedure, but not the quality of a product. Poly Processing developed our quality system over the course of 50 years, with the purpose of meeting the most challenging chemical storage tank applications — and meeting our customers’ expectations.
Our testing process is followed closely for each tank as it passes through checkpoints at specific internal departments. Each department — including process coordination, molding, quality assurance, assembly and shipping — has a hand in the quality process.
How do you know by looking at a chemical storage tank how well it’s constructed? There’s a big difference between a well-designed, properly constructed tank and an inexpensive one that doesn’t meet structural requirements. But it takes more than the naked eye to spot critical flaws.
That’s why we submit our cross-linked polyethylene tanks to five rigorous quality assurance tests. When you receive your cross-linked polyethylene tank from Poly Processing, you can rest assured that the tank has been thoroughly inspected and tested.
Let’s take a look at the Poly Processing chemical tank testing process. You can watch the video to get a better idea of how our tests are performed.
Visual Inspection
The first and most basic line of testing is the eye test. We visually inspect every tank for defects or imperfections right after it’s molded to ensure that the tank meets our rigorous quality standards.
Poly’s Quality Assurance personnel carefully inspect the tank with a fine-tooth comb. Specifically, we verify that there are no pinholes, flaws, or imperfections in the tank that could eventually lead to cracking, crazing, or brittle material.
Impact Test
The impact test is designed to test a tank’s structural integrity. A sample of the tank is collected and frozen overnight to -20 degrees Fahrenheit. It is then placed into a machine where a 20-pound “dart” is dropped from a specified height.
This test is designed to verify that the tank material can withstand mechanical stress and other challenges associated with long-term chemical storage.
Gel Test
Performed only on cross-linked polyethylene tanks, the gel test measures the percentage of cross-linking in the tank wall itself. A sample of the tank material is weighed, then placed in boiling xylene, which dissolves the linear polyethylene. The remaining sample is cross-linked polyethylene (XLPE). The sample is dried, measured, and compared to the original sample to determine the crosslink percentage. To meet ASTM standards, the tank must be at least 60% crosslinked.
Ultrasonic Test
The ultrasonic test ensures a consistent wall thickness around the entirety of the polyethylene chemical storage tank, and ensures that the tank meets the standard for its designed use. This test incorporates an ultrasound instrument to measure the wall thickness. Various points around the diameter of the tank are tested, along the entire height of the tank wall. Standard wall thickness readings are done at 0 degrees, 90 degrees, and 270 degrees at 1-foot, 2-foot, and 3-foot elevations.
Hydrostatic Test
The hydrostatic test is performed on the tank as a whole, not just a sample of the materials. It not only measures the tank’s ability to withstand hydrostatic pressure, but it measures the fittings and accessories as well.
For the hydro test, the tank is filled to the dome with water. ASTM requires that it sits for 30 minutes, but Poly Processing requires that it sits for at least 60 minutes to verify that there are no leaks in the tank or installed fittings, and that the tank can withstand the hydrostatic weight of the water. It’s common for a customer to request anything from a 4-hour to a 48-hour water test.
What Is the Documentation for This Process?
The quality assurance process is documented at the plant. The document is based on the serial number of the tank and serves as the internal checklist that accompanies the tank from department to department.
Upon request, you may receive a copy of the testing documentation. Typically, this version is an executive version of the extensive document used internally. If you want a copy of this document, Poly Processing must receive the request before the order is released.This documentation may be an additional cost as well.
A Warranty That Stands By Our Quality Testing
Poly Processing offers a five-year full warranty for tanks in most chemical applications. This includes our vertical tanks, IMFO® Tanks, double-wall SAFE-Tanks®, etc. However, our customers report that crosslinked polyethylene tanks provide 15 to 20+ years of service in many applications. In the end, though, the life of your chemical storage tank depends on several factors and variables.
Find out more about the quality of our chemical storage tanks. Contact a chemical storage tank system expert to get your questions answered.
- January 2, 2023
- Topics: Value Added
About Poly Processing
Posts By Topic
Tech Talk Podcast Episodes
Subscribe By Email
Recent Posts
- The Largest Crosslinked True Full Discharge Tanks Available: 15,500 IMFO and 15,000 Sloped Bottom IMFO
- Contained Bottom Discharge for Double-Wall Tank
- Join Us at WEFTEC 2025 Conference & Exhibition
- Effective Wastewater Treatment Chemical Storage
- How to Safely Store Sulfuric Acid to Overcome its Corrosive Nature
Tank Configurator
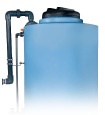
Find the recommended tank and system components for your chemical storage challenge.
Configure a Tank Package