Tank Geometry and Wall Thickness
Proper chemical storage is an important aspect of operating a plant or facility. In order to ensure that chemicals are stored safely in polyethylene tanks, you have to choose or custom-build a tank with the correct wall thickness. But what goes into determining the correct wall thickness for your chemical storage tank?
Designing a chemical storage tank with the proper wall thickness is critical to ensuring that your tank performs reliably for years, without the threat of a tank failure. If this aspect of tank design isn’t done carefully, you could end up dealing with a costly chemical leak that shuts down operations and poses safety risks.
Standard Polyethylene Tank Walls
People often ask how thick a chemical storage tank wall needs to be in a 1.65 spg tank. It will vary based on the geometry of the tank and the particular chemical that’s being stored.
It’s always important to start any tank design based on the chemical being stored and its operating temperature. In addition, typical tank thicknesses will vary based on the Specific Gravity Rating (SPG) of the tank.
Poly Processing can manufacture all of our tanks nationwide with SPGs of 1.35, 1.65, 1.9 and 2.2. The tanks can range from .20 inches thick to 1.5 inches thick, depending on their geometry and where the measurements are taken.
A 1.65 SPG tank that is very short and flat will have a thinner wall than a 1.65 SPG tank that is tall and narrow. This is because as the diameter of a tank base decreases and the height increases, the pressure on the bottom sidewall of the tank increases based on the weight of the fluid. In order to offset this weight, a thicker wall is needed to accommodate for the extra pressure that is exerted on the sidewall and floor of a tall, narrow tank.
A fluid's SPG and operating temperature are directly proportional to the weight and pressure a chemical exerts at the bottom of a tank.
Factors in Determining Wall Thickness
The formula for this geometry comes down to the allowable hoop stress, basically the force applied perpendicular to the radius of an object, of the construction material, which refers to the strength of the material at any given area of the tank sidewall. Hoop stress will be high if the tank has a small diameter, because it is measured in pounds per square inch of pressure in that tank.
A six-foot diameter tank holding the same chemical and gallonage as a twelve-foot diameter tank will have less surface area on the bottom sidewall which means it will require thicker walls to compensate for the increase in hoop stress calculated for that tank design.
Testing to Ensure Correctness in Wall Thickness
Once the necessary wall thickness is determined and the tank has been manufactured, we perform impact tests that tell us the impact strength of that particular sample of plastic. This confirms that the tank was properly cured.
We can then run ultrasonic thickness tests on different degree locations and elevations of the tank sidewall in order to determine wall thickness in specific areas. These tests ensure that the wall thickness of our tanks conform to ASTM standards and that our tanks can handle the pressure exerted from the chemical being stored.
Need to purchase a chemical storage tank? Get started with our Tank Selector Tool to custom design a chemical storage tank to fit your needs. Or check out our Tank Designs and Specifications page.
- March 10, 2025
- Topics: Tank Design and Materials
About Poly Processing
Posts By Topic
Tech Talk Podcast Episodes
Subscribe By Email
Recent Posts
Tank Configurator
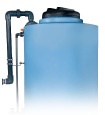
Find the recommended tank and system components for your chemical storage challenge.
Configure a Tank Package