Will Your Chemical Storage Tank Resist Environmental Stress Cracking?
Environmental stress cracking occurs in plastic tanks over time, under certain conditions. It’s a failure of the polymer material due to surface-initiated micro cracks or fractures. These micro cracks are caused by the combination of stresses and environmental effects.
The stresses and environmental effects combine synergistically to accelerate the development of these micro cracks. Even though this process is not fully understood, it is suspected that the surface active material present in the environment (a surfactant or aggressive chemical) interacts with the surface of the polymer to initiate and accelerate the formation of microscopic voids within the polymer chains.
Over time, these imperceptible cracks combine to form larger cracks or crack propagation, which can lead to leaks or even tank failure. If cracks occur, it’s recommended that you replace the polyethylene tank.
In cross-linked polyethylene (XLPE) tanks, tank cracking can produce very small leaks over time. In high-density linear polyethylene tanks (HDPE), mechanical stress can lead to catastrophic failure. If a crack develops due to this stress in an XLPE tank, the cross-linked polymer chains provide a safeguard to help prevent further splitting—unlike potential “unzipping” that can occur in HDPE tanks.
Polyethylene’s resistance to these cracks is called environmental stress crack resistance (ESCR), and it’s a critical factor in the design and testing of polyethylene chemical storage tanks. Whether they be single wall vertical tanks, IMFO® tanks, or double wall SAFE-Tanks®, the material used in the chemical tanks must have a high level of ESCR for long term performance in end use applications.
How Stress Cracks Occur
Traditionally, when polyethylene is processed, it is done via common plastics processes such as injection molding, extrusion, thermoforming, or blow molding. These processes themselves produce stress because of the pressures, cooling rates, and molecular orientation that are involved in the storage tank manufacturing process. This molded-in stress can result in a possible failure point where the tank is weakest.
In contrast, Poly Processing’s rotational molding creates a virtually stress-free product. However, other factors can lead to environmental stress cracking, such as exposure to harsh chemicals, extreme temperatures, high pressure, and environmental elements.
You can minimize this risk by choosing the right tank materials and following Poly Processing’s installation and operation guidelines.
Chemicals like soaps, detergents, and wetting agents or surfactants are particularly hard on polyethylene, causing cracking over time. And because polyethylene tanks also expand and contract with the cycling of the tank, they can experience operational stress during chemical discharge or filling.
Fortunately, ESCR tests can validate the strength of a polyethylene tank and measure its resiliency to cracking. These tank tests ensure that the tank’s materials and composition meet the safety standards necessary for chemical storage tanks.
Environmental Stress Crack Resistance (ESCR) Test
The most common environmental stress crack resistance test is the ASTM D-1693 Standard, which is the standard test method for ethylene plastics. This test determines the susceptibility of a particular polyethylene to stress cracking when storing surfactants. This helps ensure that the polyethylene will perform as it should over time for a safe and durable chemical storage tank.
During the test, 10 1/8 inch-thick samples of compression-molded polyethylene are placed under stress. The plastic pieces, or samples, are given a controlled imperfection or notched to create the samples. They are bent and inserted into a bending clamp to keep them stressed. The samples are then placed in an aggressive surfactant, at an elevated temperature, and monitored.
Measuring ESCR Test Results
Results are measured hourly. If a sample cracks, it usually cracks perpendicular to the notch. Samples that crack fail the resistance test. Each of the ten samples represents 10% of the sample group. The test is typically stopped when the sample group reaches a 50% failure rate.
The ASTM D-1693 has proven that XLPE has excellent stress crack resistance. It can hold up under stress and surfactant exposure with zero failures for thousands of hours. In contrast, HDPE samples typically last less than a hundred hours when tested at the harshest conditions.
Learn more about ESCR with our white paper, "Understanding Environmental Stress Crack Resistance (ESCR) in Rotomolded Polyethylene Tanks."
Poly Processing’s engineers will work with you to ensure that your particular chemical storage tank system will be designed to withstand environmental stress and give you the longest useful life possible. To properly design a polyethylene tank for your specific application, talk to a chemical storage expert today.
- August 12, 2024
- Topics: Value Added, Tank Design and Materials, FAQs
About Poly Processing
Posts By Topic
Tech Talk Podcast Episodes
Subscribe By Email
Recent Posts
Tank Configurator
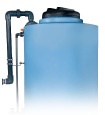
Find the recommended tank and system components for your chemical storage challenge.
Configure a Tank Package