[Featured in ES&E Magazine] How To Build Cost-Effective Storage Solutions For Wastewater Treatment Chemicals
In addition to physical and biological treatment, wastewater treatment requires aggressive usage of large amounts of chemicals, so safe storage of them is always an important consideration.
To facilitate the removal of solid particles within wastewater, chemicals such as ferric chloride, polymers and alums are used to produce positive charges. These are intended to neutralize negatively charged solid particles. As a result, the solid particles clump together, making removal easier. Since more solids exist in wastewater than municipal drinking water, more chemicals are required for this coagulation process.
Neutralization, or the adjustment of the pH levels of wastewater with the addition of an acid or a base, is common in wastewater treatment. Either sulfuric acid or another base chemical (typically sodium hydroxide) may be added to the water to achieve optimal pH balance.
The collection and treatment of industrial wastewater can result in some unpleasant odors. Chemical treatment is used to control them, in addition to activated carbon and wet scrubbers. It is very common to see sodium hydroxide, calcium nitrate and hydrochloric acid used in these processes.
To prevent the spread of disease, microorganisms that are pathogens must be destroyed or removed from wastewater. A common, relatively safe, and inexpensive disinfecting chemical is sodium hypochlorite.
Finally, a polymer chemical is typically used to remove water from sludge to reduce volume, making transporting the sludge to the landfill easier and less expensive.
Chemical Storage Systems
Every chemical storage system that is built should start with the chemical involved. Thoroughly understanding the nuances of the chemical’s properties is vital to maximize the operation and performance of the chemical delivery system, as well as the longevity of the chemical storage tank.
The storage tank is the headworks of the system, so it is a critical component of the overall process involving the use of the chemical. If the design of the storage tank is wrong, it could lead to serious problems. If you simply design a tank based on generic factors such as size, material and capacity without defining the chemical used, you risk getting a non-optimal tank.
Also, it is important to consider the effect that chemical properties have on the other component parts of the storage system. Valves, fittings, pumps and flow meters—all essential parts for proper operation—could potentially be compromised.
Sodium Hypochlorite
Sodium hypochlorite is one of the most common chemicals used to eliminate bacteria and viruses, especially towards the end of the process, in the disinfection stage.
It presents several major chemical storage challenges, including breakdown under UV light exposure; the fact that it tends to contain transition metals such as nickel, iron and copper that accumulate in the tank and create off-gassing exposure; and that it aggressively oxidizes.
Since sodium hypochlorite is an aggressive oxidizer, the opportunity for it to escape the storage tank must be limited through wetted connections and side fittings. This will reduce leak paths that can cause damage. In addition to oxidation, sodium hypochlorite is sensitive to transition metals found in some common tank fittings. These will quickly degrade the chemical, while causing off-gassing and even more aggressive oxidation.
One key to storing sodium hypochlorite is to use carbon black, white, or gray compound cross-linked polyethylene (XLPE) resin to dramatically reduce UV degradation of the chemical, as well as mastic coatings and insulation. XLPE is excellent for strength and chemical compatibility, and using an antioxidant inner resin prevents oxidation. This combination seamlessly bonds the engineered interior antioxidation resin with a maximum strength outer surface.
To prevent the potential buildup of transition metals in the tank, a molded, full discharge fitting like the Poly Processing IMFO® system must be used. This special, integrated flange is molded into the tank, preventing chemical contact with any surfaces other than polyethylene. It also allows for full discharge/ drainage of the tank, which can greatly increase the half-life of the chemical. Any additional fittings should be PVC.
Any gaskets should be made of EDPM or Viton GF to meet NSF-61 Certification. Should bolts be needed, titanium is a good choice, in order to mitigate the risk of off-gassing
Sulfuric Acid
Sulfuric acid is the most commonly used acid in the world, and is often used during wastewater neutralization. Proper storage presents two main challenges: the weight of the chemical, and its nature as an aggressive oxidizer.
The inherent weight of sulfuric acid requires a strong material to withstand the static load pressure pushing on the bottom third of the storage tank. When storing sulfuric acid, it is important to verify the hoop stress rating and understand specific gravity ratings, ensuring the resins used in the storage tank provide a margin of safety. Volume changes and temperature variations affect the tank walls as well. In addition, the concentration weight will limit the size of the storage tank.
Sulfuric acid is also an aggressive oxidizer, meaning safeguards are required to prevent structural degradation of the tank’s polyethylene material. Such damage can result in leaks or failure of the tank.
The molecular strength of XLPE and thicker tank walls can provide the structural support required for storing this heavy chemical. These aspects are particularly important in the bottom third of the tank, where high levels of load are concentrated.
If secondary containment is present, a molded full discharge fitting instead of mechanical fittings, will maximize the tank’s structural integrity. Combining this tank design with an antioxidant resin system will reduce oxidation dramatically.
If secondary containment is not present, a double wall system is recommended. Along with containing the chemical from its surrounding environment, these double-walled tanks greatly lower the risk of hazardous contact of sulfuric acid with water.
Ferric Chloride, Aluminum Chloride and Polymers
Polymers are used in the headworks of wastewater treatment to facilitate flocculation. They also aid in the dewatering of digester cake, thus reducing the volume of waste materials needed to be disposed of. Because polymers are very slippery chemicals, there is always a danger of slips and falls resulting from spills or leaks. In addition, polymers can be an environmental stress crack agent.
A full discharge fitting system is ideal for sludge control and ease of cleaning, since the tank drains at its true bottom. Heat pads and insulation can help keep the chemicals at the optimal temperature, greatly reducing the chance of separation and settling.
Using XLPE tanks will allow for greater expansion and contraction, while maintaining structural integrity, and thus lessening the risk for tank failure. A mixing system can also be installed to keep the chemicals from separating.
Tanks for these types of chemicals require titanium bolt material, while stainless steel bolts should be used for aluminum sulfate and various other polymers. A SAFE Surge® manway cover is recommended on pneumatically loaded systems to support tank longevity
Sodium Hydroxide
Sodium hydroxide is commonly used in wastewater treatment to adjust or neutralize the base pH levels. Similar in use to sulfuric acid, it can balance the wastewater pH. Sodium hydroxide is another “slippery” chemical that tends to find weak points under storage. It is also highly corrosive to human skin and toxic if ingested, making exposure to workers a potential danger.
In addition, if sodium hydroxide is not stored at appropriate temperatures, the chemical will crystallize and turn into a solid. This results in unnecessary chemical waste and damage to the storage system itself.
The key to storing sodium hydroxide properly is strong, safe containment. Since the chemical is so corrosive, secondary containment is a must. If secondary containment is available, a full discharge tank is recommended. Full discharge fitting systems are ideal for sodium hydroxide systems because their flange is a molded part of the tank and not an insert that could leak or fail.
A full discharge outlet eliminates the need to drill into the sidewall of the tank to install a mechanical fitting, which can create a maintenance issue for this chemical, thus ensuring long-term performance of the overall system.
When secondary containment is not available, a properly designed double wall tank like the Poly Processing SAFETank® can meet this requirement. This double-walled tank extends the margin of safety by providing 110% secondary containment. These tanks can be double-wall piped safely, using a transition fitting with a built-in expansion joint.
Hydrochloric Acid
Hydrochloric acid is a pungent liquid with highly corrosive properties. While hydrochloric acid has several different applications, in wastewater treatment it is used to control odours that come from industrial wastewater.
With an extremely low pH, it is highly corrosive and can generate toxic fumes that can be harmful or fatal. These fumes also present a maintenance issue, as entering the tank for cleaning must be avoided and parts replacement minimized.
An integrally molded flanged outlet (IMFO®) allows for complete drainage of the tank, which eliminates the need to enter the tank for cleaning. It also reduces the chances of having to replace parts, as the drainage system is part of the tank’s mold. This is imperative when dealing with such a strongly fuming chemical.
Scrubber systems are used to control the fumes. No restraint or ladder attachment bands circumscribing the tank are allowed. Cable restraint systems must pass cables over the top of the tank. Hydrochloric acid requires the use of flexible connections with fittings on the lower third of the sidewall.
Conclusion
When it comes to protecting your equipment, your personnel, and your chemical supplies, cross-linked polyethylene tank systems are second to none. Not only are they a smart financial investment, but they can also outperform other tank options for reliability, safety and longevity.
- November 13, 2023
About Poly Processing
Posts By Topic
Tech Talk Podcast Episodes
Subscribe By Email
Recent Posts
- Join Us at WEFTEC 2025 Conference & Exhibition
- Effective Wastewater Treatment Chemical Storage
- How to Safely Store Sulfuric Acid to Overcome its Corrosive Nature
- The Complete Journey of Owning and Retiring a Polyethylene Storage Tank
- Is Polyethylene a Storage Solution for Elevated Temperature Tanks?
Tank Configurator
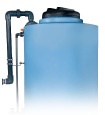
Find the recommended tank and system components for your chemical storage challenge.
Configure a Tank Package