Flocculation Chemical Storage for Water Treatment
Coagulation is one of the preliminary steps in treating wastewater to make it safe for drinking. When chemicals are used, proper design and engineering of the storage tank can help ensure safety, longevity, and operational efficiency.
As you configure your coagulant storage system, it’s important to understand how coagulants work in wastewater treatment, what to do about the sludge that accumulates, and how to minimize risks.
Understanding Coagulation and Flocculation
Most water sources contain small floating particles that must be removed to help make the water potable. These floating particles, called colloids, are too light to settle by gravity. They are made up of both non-organics (such as clay or silt) and organics (such as algae or bacteria). When ingested by humans, some of the colloids can be fatal.
A practical way to deal with colloids is to settle these particles out of suspension by bonding them to one another so that they become heavy enough to settle by gravity. This process of bringing the particles together is called flocculation.
After the floc forms, it can be separated, which leaves you with clear water. This is known as coagulation. The chemicals that cause these particles to cling together and fall out of suspension are called coagulants, or flocculants.
Flocculant and Coagulant Chemicals
Almost all colloids have negatively charged surfaces. Introducing charged particles (with positive ions) to the water attracts the colloids, like opposite poles of a magnet. Two common coagulation chemical groups (both metal salts) are used to clump solids together in the water stream today.
Those based on aluminum:
- Aluminum sulfate (or Alum) Al2(SO4)3
- Polyaluminum Chloride
- Aluminum chloride
- Sodium aluminate
Those based on iron:
- Ferric sulfate (iron sulfate) Fe2(SO4)3
- Ferrous sulfate
- Ferric chloride (2x times the iron content of Ferrous Sulfate)
Other chemicals used as coagulants include hydrated lime and magnesium carbonate.
Water Treatment Tank Design Considerations
In order to configure a safe and effective coagulation storage solution, you will need to consider several factors that will impact your chemical storage system.
Sludge
Metal chemicals (alum or ferric) can cause sludge to build up in the bottom of a storage tank. This concentrated sludge can even become radioactive, and some state departments of environmental quality require special hazardous waste removal of old coagulant tanks.
A full discharge is necessary to alleviate this build up and to ensure a safe and clean tank. Some facilities simply install an outlet above the tank bottom so that sludge can settle below the pump feed, but this can exacerbate the problem.
Poly Processing’s Integrally Molded Flanged Outlet® (IMFO®) allows the tank’s contents to discharge flush to the bottom of the tank. This outlet is integrally molded into the sidewall during manufacturing, eliminating leak concerns where other full drain options use welds, inserts, or attachments that can fail. Poly Processing has also developed a sloped bottom version of the IMFO tank system. The sloped bottom tank system greatly minimizes the hazards associated with traditional vertical tank maintenance. With Poly Processing’s Sloped Bottom Integrally Molded Flanged Outlet tank, or IMFO® system, the floor of the tank is sloped towards the IMFO giving the user the greatest possible full discharge system in a vertical tank design.
Temperature
In addition to choosing a tank with a full discharge, it’s also important to choose a chemical storage solution that can handle elevated temperatures. Alum is frequently delivered at temperatures as high as 120°F (52°C). Cross-linked polyethylene (XLPE) tanks have better temperature limits than a standard linear polyethylene (HDPE) storage tank.
For harsh environments, a steel tank lined with polyethylene such as PolyGard will provide extended tank life.
Likewise, in some cases the unwanted crystallization of coagulants can occur at lower temperatures. You may want to consider installing your tank indoors or possibly including a heat trace and insulation system to maintain the correct temperature if necessary.
With a proper review of the application by a chemical tank specialist, a high-density cross-linked polyethylene tank system can last for many years and deliver a performance that is far superior to other systems.
Level Indication
Polyethylene chemical storage tanks are usually translucent enough to provide a visible indication of the liquid level. However, when these tanks must be insulated, or where other types of coagulant storage systems are used, alternative methods are available.
We recommend using a reverse float level gauge as a safe and economic option. The float gauge is highly visible and won’t introduce potential leak issues that can be caused by tank wall penetrations.
Poly Processing’s reverse float level gauge consists of a float inside the tank, which bobs on the surface of the chemical. The float is compatible with any kind of chemical that can be stored in a Poly Processing tank. The float is attached to a rope, which travels through a clear vertical pipe on the outside of the tank. A level indicator is attached to the end of the rope.
As the tank is filled, the chemical lifts the float inside the storage tank, and the level indicator on the outside is lowered. As a reverse gauge, the level indicator shows the reverse of a tank’s level—the lower the indicator, the fuller the tank.
The reverse level gauge uses a pulley system with polypropylene rope, nylon rollers inside of PVC elbows, clear pipe, and a level indicator. The external components are dry-fit together, not glued. Assembling and replacing the gauge is easy and only takes a few minutes. Maintenance is simple, and individual pieces can be replaced, if needed.
Filling Your Coagulant Tank
It’s important to note that some coagulants, such as polymers, can be quite viscous. This means that there can be problems with filling a coagulant tank using a downpipe.
When the alum is pushed into the bottom of the tank with pneumatic pressure from a tanker truck, the contents can bubble, causing heavy pressure buildup under the fluid and resulting in a jackhammer effect that creates stress on the sidewalls, even causing the entire tank to jump.
Fill pipes in these installations should always end above the highest fluid level of the tank.
You can also incorporate an anti-foaming connection that directs the chemical to hit the top sidewall and run down the interior tank wall, preventing foaming and splashing while still removing the need for a downpipe.
To get more information on coagulant and flocculant storage tanks, talk to a chemical storage expert today.
- November 21, 2022
- Topics: Applications
About Poly Processing
Posts By Topic
Tech Talk Podcast Episodes
Subscribe By Email
Recent Posts
- The Largest Crosslinked True Full Discharge Tanks Available: 15,500 IMFO and 15,000 Sloped Bottom IMFO
- Contained Bottom Discharge for Double-Wall Tank
- Join Us at WEFTEC 2025 Conference & Exhibition
- Effective Wastewater Treatment Chemical Storage
- How to Safely Store Sulfuric Acid to Overcome its Corrosive Nature
Tank Configurator
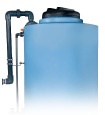
Find the recommended tank and system components for your chemical storage challenge.
Configure a Tank Package