The Two Main Steps of the Wastewater Treatment Process
Wastewater treatment is an extremely important part of making sure that humans treat the earth with respect. The proper treatment of wastewater is essential not only for the environment — due to the use of several chemicals throughout the process, a safe process also keeps employees and your facility safe.
Wastewater treatment is usually broken down into two sections: primary treatment, which removes grease, dirt, gravel, and floatable waste, and secondary treatment, which removes even more suspended solids and pollutants by using biological processes.
Primary Treatment
During primary treatment, 40-50% of solids are removed from wastewater. This process usually involves large screens that let water pass through, but not floatable trash and other pollutants. These materials are collected and then properly disposed of.
The next part of primary treatment involves the filtration of water through a grit chamber, which allows for the removal of coarse solids like bits of rock, metal, bone, and other larger pieces from the water. This is done for two primary reasons: to keep the water clean, and to prevent the grit from causing damage to the equipment used in wastewater treatment.
The last step of primary treatment involves sedimentation, which causes the physical settling of matter. Sedimentation often uses chemicals like flocculants and coagulants.
Secondary Treatment
The second of the main steps of wastewater treatment is usually the final step to wastewater treatment. It generally removes 85-90% of all the pollutants. During secondary treatment, water flows through a secondary sedimentation tank that allows both solid wastes and microorganisms to form clumps and settle out of the water that is being treated.
This step in the process of wastewater treatment uses various types of bacteria to treat water. A part of the mixture of solid wastes and microorganisms that join together can be mixed with air and reused: this combination is called “activated sludge.” Activated sludge can be used to help improve crop soil or as a component of the process of making methane gas.
Once the water moves past this stage, it enters into the disinfection stage. During this part of the wastewater treatment process, chemicals like chlorine and sodium hypochlorite are added to the wastewater to remove harmful pathogens that cause cholera, polio, typhoid, and other diseases.
Once the wastewater finishes its treatment, it can be returned safely to waterways in the vicinity where it will become a part of the natural environment and provide a home for fish and other types of water-based plants and animals.
Tertiary Treatment
These main steps of wastewater treatment are the most important, but there is a third step known as tertiary treatment. It is not as common as the other two steps, but tertiary treatment is capable of removing over 99% of all impurities from wastewater. Unfortunately, tertiary wastewater treatment is also relatively expensive.
Ensuring Safety During The Treatment Process
It’s important that your facility does everything in its power to help this process. By operating your wastewater plant in a safe way, you can help ensure you are running a more effective wastewater treatment plant, while keeping your facility, your employees, and the environment safe.
One of the best ways to ensure safety of the people and environment around you is to think through proper chemical storage. Our best advice is to start with the chemical you will be storing. You’ll be using different chemicals for at least five different reasons throughout the process, and each chemical requires specific storage guidelines be met.
Poly Processing Can Help
Poly Processing is a manufacturer of high-performance tank systems and is dedicated to cost effective storage system safety and innovation. Safety, longevity, and ease of use are crucial to every tank we build. A few of our innovative solutions include the IMFO® and Sloped Bottom IMFO full discharge tank systems, SAFE-Tank® double wall tank, OR-1000™ System, and XLPE tanks.
Poly Processing serves water and wastewater, agricultural, industrial, alcohol, dairy, manufacturing, oil, gas, pharmaceutical, pulp, paper, power, food and beverage, as well as many other industries. You don't get to be the leader in chemical storage tank manufacturing and tank systems unless you're also constantly innovating better solutions. Poly Processing is constantly pushing the envelope to develop new products and to improve existing chemical storage solutions.
Not only do we continually strive to introduce new solutions that no other tank manufacturer can offer, we also aim to develop new products that outperform our current ones.
Poly Processing custom manufactures cross-linked polyethylene storage tanks to fit the unique needs of our customers. We'll help you design a chemical storage solution that's manufactured with our own innovations — just the ones you need, and none that you don't.
We’re the leader in building innovative solutions to complex chemical storage challenges. Far beyond simple plastic tanks, we have developed a fleet of products that address a wide range of specific issues related to chemical storage.
The result for your business is greater ease of use, increased safety and environmental care, easy tank maintenance, and extended tank longevity.
Discover how we've set ourselves apart and the groundbreaking technology we've produced — explore each of Poly Processing's industry-leading storage tank innovations.
- September 16, 2024
- Topics: Applications
About Poly Processing
Posts By Topic
Tech Talk Podcast Episodes
Subscribe By Email
Recent Posts
- Join Us at WEFTEC 2025 Conference & Exhibition
- Effective Wastewater Treatment Chemical Storage
- How to Safely Store Sulfuric Acid to Overcome its Corrosive Nature
- The Complete Journey of Owning and Retiring a Polyethylene Storage Tank
- Is Polyethylene a Storage Solution for Elevated Temperature Tanks?
Tank Configurator
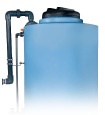
Find the recommended tank and system components for your chemical storage challenge.
Configure a Tank Package