How Mechanical Stress Can Cause Tanks to Crack
We’ve written several articles about the importance of protecting your chemical storage tank from aggressive chemicals. Mechanical stress can be just as significant, causing polyethylene chemical storage tanks to crack. Mechanical stress occurs when the tank’s structure is compromised after a physical impact with another object, over pressurization, improper venting, or rigid plumbing that doesn’t allow natural expansion and contraction of the tank.
In cross-linked polyethylene (XLPE) tanks, tank cracking can produce small leaks. In linear polyethylene tanks, mechanical stress can lead to catastrophic failure. If a crack develops due to this stress in an XLPE tank, the cross-linked polymer chains provide a safeguard to help prevent further splitting—unlike potential “unzipping” that can occur in linear polyethylene tanks.
In this article, we’ll look at factors that cause stress cracking in polyethylene storage tanks and offer solutions to reduce the impact of mechanical stress.
Mechanical Stress in Polyethylene Storage Tanks
Any time you put a hole in a tank, it can provide an opportunity for stress cracking. The most common cause of mechanical stress in a polyethylene chemical storage tank comes from cutting a hole in the storage tank sidewall to accommodate fittings. When a hole is created and a fitting is attached, a binding effect is created, causing a cantilevering action.
As a result, the polyethylene tank wall expands and contracts under stress. Rather than allowing the tank to expand and contract naturally, cracks can develop near the fitting holes. This makes flexible connections vital to a successful storage system.
We recommend putting sidewall fittings in a tank only when necessary — and don’t add any fittings that you don’t need. With cross-linked polyethylene, the polymer chains are bonded around the hole to minimize the risks.
Fittings should always be positioned above the knuckle radius where the wall thickness is most even. This allows the tank to expand and contract without causing the fitting bolts to bind in the area of the cut or drilled holes.
Poly Processing's IMFO® Tank can eliminate the need for sidewall penetration altogether. The Integrally Molded Flanged Outlet® (IMFO) full discharge system is a homogenous flange that is molded at the bottom sidewall as part of the tank during manufacture, making it a stress-free part of the tank. The flange is created from the same material as the tank — it’s not a metal insert added during or post-production.
Benefits of the innovative IMFO Tank include:
- Full tank discharge, because the flange is at the bottom of the sidewall, below the tank knuckle radius. There’s no need to enter the tank for cleaning.
- Enhanced long-term performance and greater useful life of the tank since the flange doesn’t compromise the tank’s hoop integrity or structural design.
- Complete flange face protection in aggressive oxidation environments. The antioxidant OR-1000™ system protects the discharge components from deterioration.
- Highest amount of static head pressure. The IMFO’s design brings you the highest net positive suction head (NPSH) of any vertical non-coned tank on the market.
- Any required maintenance is simple and hassle-free. Unlike metallic inserts, the flange extends away from the tank wall and the entire flange system is external with easy hardware access from outside the tank.
- No chemical compatibility issues like the ones you may encounter with metallic inserts. If the chemical is safe in a crosslinked polyethylene tank, it’s safe discharging out of the IMFO system.
It's also important to use flexible connections or expansion joints with the correct performance specifications to allow for tank expansion and contraction. Poly Processing's team of chemical storage tank experts can assist in getting you the right fittings, proper plumbing, venting, and accessories needed to provide the longevity you expect with a cross-linked polyethylene tank.
Manufacturing Robust Storage Tanks
The American Society for Testing and Materials (ASTM) has established four tests for cross-linked polyethylene tanks to help reduce the possibility of stress cracking. These tests ensure that the tank’s materials and composition meet the safety standards necessary for chemical storage tanks.
One of those tests, the ASTM Gel Test, provides a precise measurement of the concentration of cross-linked resin in a polyethylene tank. More cross-linked polymers provide a stronger molecular bond and greater resistance to mechanical stress. Poly Processing tests a sampling of our tanks to ensure that we’re consistently manufacturing XLPE tanks that meet or exceed the ASTM standards and will provide the stress resistance you need.
The Gel Test is performed after a tank is molded. We cut a small 1/8” sample out of the interior tank wall and weigh the sample. We use a piece of the interior tank wall because that’s where the polyethylene will interact with the chemical. After weighing, the sample is boiled in a chemical solution, which strips away all of the resin that isn’t cross-linked.
The remaining sample is weighed and compared to the original weight. By doing a simple percentage calculation of the remaining weight of the tank sample, we get a reading on the tank’s gel percentage and structural integrity.
The ASTM Gel Test requires that the percentage of cross-linked resin in a polyethylene tank must be 60% or greater at the innermost 1/8” of the tank wall. Anything less is unacceptable and would result in a structurally unsound tank.
It’s one thing to say XLPE polyethylene tanks perform better mechanically — it’s another thing to really put them to the test. To find out if our crosslinked polyethylene tanks would hold up under real-world mechanical stresses, we subjected cross-linked and linear high-density polyethylene tanks to strenuous test conditions. The results were impressive.
The video below shows the drop test video of 3000 gallon tanks with 7,000 pounds of water dropped from heights up to 45 feet to a concrete surface.
Proper Venting Extends Chemical Storage Tank Life
Often, the importance of venting is overlooked as a very important step that reduces stress on the tank and promotes tank longevity. A crucial factor impacting the safe operation of the poly chemical storage tank and maximizing the useful life of the tank is proper and safe venting of the tank.
Polyethylene tanks are rated at atmospheric pressure/vacuum. Adequate vent size is always based on flow and delivery rates, so it is important to gather the following information to adequately determine the proper venting requirements:
- Is the tank to be filled pneumatically?
- Is the tank to be vented into the atmosphere?
- Does the length of the vent exceed 3 feet (piped to a central vent system)?
- Is a fume scrubbing system to be used?
- Are vent screens to be used (restricts flow)?
- Does the tank manufacturer offer a method of “emergency venting” to prevent over pressurization?
Contact a Poly Processing storage tank specialist to see how you can minimize the impact of mechanical stress and increase the useful life of your own chemical storage tanks.
- January 20, 2025
- Topics: Value Added
About Poly Processing
Posts By Topic
Tech Talk Podcast Episodes
Subscribe By Email
Recent Posts
- The Largest Crosslinked True Full Discharge Tanks Available: 15,500 IMFO and 15,000 Sloped Bottom IMFO
- Contained Bottom Discharge for Double-Wall Tank
- Join Us at WEFTEC 2025 Conference & Exhibition
- Effective Wastewater Treatment Chemical Storage
- How to Safely Store Sulfuric Acid to Overcome its Corrosive Nature
Tank Configurator
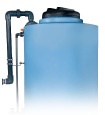
Find the recommended tank and system components for your chemical storage challenge.
Configure a Tank Package