Sodium Hypochlorite Storage Considerations and Solutions
Sodium hypochlorite is a chemical used in thousands of applications. It is one of the most common chemicals used in water treatment to eliminate bacteria and viruses from drinking water supplies. By no means is it limited to just public works, any environment that requires sanitation from industrial to food processing find it to beneficial. As an aggressive oxidizer, it can even be used in manufacturing paper products to bleach and oxidize fibers.
While sodium hypochlorite is a commonly used chemical, it does present unique storage challenges. Let’s examine the storage considerations and solutions for sodium hypochlorite.
Storage Considerations for Sodium Hypochlorite
Since sodium hypochlorite is an aggressive oxidizer, the opportunity for the chemical to escape the storage tank must be limited. The number of wetted connections and fittings on the side of the tank must be minimized to reduce leak paths which can damage a tank.
In addition to oxidation, sodium hypochlorite is sensitive to transition metals. Transition metals will quickly degrade the chemical and cause off-gassing and even more aggressive oxidation.
Sodium Hypochlorite Storage Solutions
To minimize the potential for oxidation, chemical storage tank sidewall fittings and connections must be minimized. Poly Processing’s innovative solution to minimize bulkhead and traditional sidewall fittings, and reduce potential leaks that develop from oxidation, is the Integrally Molded Flanged Outlet, or IMFO® system. Since the full drain flange is molded into the polyethylene plastic tank, the potential for leaks that lead to cracks from oxidation is minimized. In addition, with the IMFO system, gaskets on the bulkhead fitting can be maintained from the exterior of the polyethylene tank.
The IMFO system also makes full tank draining feasible which allows transition metals to be flushed out of the tank before refill.
An additional Poly Processing innovation for storage of sodium hypochlorite is the exclusive OR-
1000 system. OR-1000’s engineered inner surface is made of medium-density polyethylene, specifically formulated to resist oxidation. Its outer surface is made of XLPE, high-density crosslinked polyethylene, for superior strength. The two surfaces are molecularly bound together during the roto-molding process, creating a truly seamless bond between the XLPE and the inner surface of the polyethylene tank.
With the IMFO, full tank drainage is accomplished, and the one-piece molded tank construction minimizes the need for any other sidewall connections. In addition, the OR-1000 minimizes the potential for oxidation to the wetted surfaces of the tank. With this one-two punch, Poly Processing offers the superior storage solution for sodium hypochlorite. Poly Processing is the only company to offer a published warranty for sodium hypochlorite storage systems over one year.
If a five-year published warranty and long tank life makes sense for your sodium hypochlorite storage needs, download the sodium hypochlorite storage system guide for more information or contact a Poly Processing chemical storage tank expert.
- May 20, 2013
- Topics: Chemicals
About Poly Processing
Posts By Topic
Tech Talk Podcast Episodes
Subscribe By Email
Recent Posts
- The Largest Crosslinked True Full Discharge Tanks Available: 15,500 IMFO and 15,000 Sloped Bottom IMFO
- Contained Bottom Discharge for Double-Wall Tank
- Join Us at WEFTEC 2025 Conference & Exhibition
- Effective Wastewater Treatment Chemical Storage
- How to Safely Store Sulfuric Acid to Overcome its Corrosive Nature
Tank Configurator
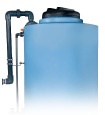
Find the recommended tank and system components for your chemical storage challenge.
Configure a Tank Package