How to Make Sure Your Tank’s Walls Are Thick Enough
Proper chemical storage is an important aspect of operating a plant or facility. In order to ensure that your chemicals are stored safely in polyethylene tanks, you need to choose a tank with the correct wall thickness. A fraction of an inch can make the difference between a tank that lasts for decades and one that fails early.
Here’s what you need to know about determining the correct wall thickness for your chemical storage tank.
Factors Affecting Your Tank’s Walls
Wall thickness varies from tank to tank, based on several factors that all come into play, including:
- Chemical being stored
- Operating temperature of the chemical
- Dimensions of the tank
The chemical itself, and its operating temperature, determine a tank’s specific gravity rating (SPG). Chemicals that are dense and warm have a higher specific gravity than lighter, cooler chemicals. Your tank needs to be rated for the correct specific gravity, or it could fail. We manufacture our standard tanks with SPGs of 1.35, 1.65, 1.9 and 2.2.
A fluid’s SPG and operating temperature are directly proportional to the weight and pressure the chemical exerts at the bottom sidewall of a tank. Customers often ask how thick a chemical storage tank wall needs to be in a 1.65 SPG tank. It will vary based on the geometry of the tank, and our engineers can work with you to determine what you need.
Tank walls can range from .20 inches thick to 2 inches thick or thicker, depending on size, dimensions, and where the measurements are taken. A 1.65 SPG tank that is very short and flat will have a thinner wall than a 1.65 SPG tank that is tall and narrow. That’s because of the third factor, size dimensions. As the diameter of a tank base decreases and the height increases, the pressure on the bottom sidewall of the tank increases. As a result, you need a thicker wall to handle the extra pressure on the sidewall of the tank.
Calculating Wall Thickness
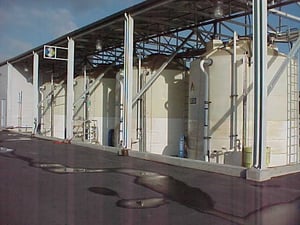
The calculation for this geometry comes down to the allowable hoop stress of the construction material. Hoop stress is the force applied to the tank wall from inside the tank. Hoop stress is higher on a tall tank with a small diameter, because it is measured in pounds per square inch of pressure in that tank.
A six-foot diameter tank holding the same chemical and gallonage as a twelve-foot diameter tank will have less surface area on the bottom sidewall, so it will require thicker walls to compensate for the greater hoop stress. We make our calculations and design each tank based on the ASTM D 1998-13 standards. You can download an explanation of the ASTM standard for more information.
Testing Wall Thickness
Poly Processing regularly tests our tanks to ensure that the wall thickness conforms to ASTM standards and that our tanks can handle the pressure from the chemical you’re storing. We take these tests seriously so that you can rest assured that your chemical storage tank will perform at or beyond expectations.
Once a tank has been manufactured, we perform impact tests to determine the impact strength of the tank and confirm that the tank was properly cured. We can also run ultrasonic thickness tests on different locations and elevations of the tank sidewall to determine wall thickness in specific areas.
If you have questions about designing your tank for proper wall thickness, contact one of our chemical storage experts.
- July 25, 2018
- Topics: Tank Design and Materials
About Poly Processing
Posts By Topic
Tech Talk Podcast Episodes
Subscribe By Email
Recent Posts
Tank Configurator
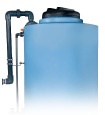
Find the recommended tank and system components for your chemical storage challenge.
Configure a Tank Package