Do You Need to Use Baffles for Tank Mixing Applications?
Mixing chemicals and other substances is a lot like mixing cake batter. A container is involved, as is a stand (or bracket) to support the mixing system. But, if you’ve ever made a cake, you know that you have to move the bowl around to mix all the ingredients. It doesn’t work to stick the beaters down in the bowl and keep them in one place.
Obviously, in a chemical storage and mixing scenario, moving the tank around to get all the chemical that can’t be reached is not an option. That's where proper mixer setup comes in.
What Are Baffles and Do You Need Them?
Baffles are long, flat plates that attach to the inside of your chemical storage tank to help prevent swirling and promote top-to-bottom fluid movement. They are most commonly used for blending and solid suspensions, because these applications often use vertical cylindrical tanks that tend to create swirling patterns.
In many cases however, baffles are not needed if the mixer is properly installed with the shaft and impeller at the correct angle, rpm, impeller size and depth. Poly Processing strongly recommends contacting one of our partners who represent high quality industrial mixer companies to get the most effective and reliable system for your application.
Three or four baffles are typically used in a tank, depending on its size, and they are mounted 4-6 inches off the inside of the wall.
How are Baffles Attached to XLPE Tanks?
Baffles aren’t welded to the inside of a crosslinked polyethylene (XLPE) tank. Instead, they’re installed with polyethylene encapsulated bolts and closed with a gasket to prevent leaks. These are the same bolts that are used for internal/external pipe support. The gasket material is dictated by the type of chemical you’re storing.
Since the baffles are made from polyethylene and are bolted onto polyethylene, there are no concerns about chemical compatibility.
Chemical Mixing Considerations
Different chemicals require different chemical mixing systems. Some solutions create sludge, and the sludge needs to be mixed to avoid buildup at the bottom of the tank. Mixers can also be installed at an angle to create a different mixing pattern.
Some food, pharmaceutical, and wastewater applications require a clean in place (CIP) application to prevent contamination.
Designing Your Chemical Mixing System
Poly Processing offers several different styles of chemical mixer mounts, depending on the mixer configuration:
- Clamp-on Style Mixer Attachment – Used on small vertical storage tanks with very small and lightweight mixers
- Small Freestanding Mixer Support – Used on small open top chemical tanks with small and lightweight mixers
- Vertical Tank Supported Mixer Bridge – Used on smaller vertical tanks
- Large Vertical or Open Top Tank Freestanding Mixer Bridge – Used on vertical tanks and open top tanks with larger mixers
When designing your chemical tank mixing system, it’s critical to consider several factors to ensure that the proper bracketing is used. Engineers need to determine the downward load, bending load, weight of the mixer, torque load on the mixer, and the angles. Careful consideration and understanding of these elements ensures you have a safe, cost effective chemical storage solution.
However, when a mixer is not properly mounted and bracketed, improper mixing can result in additional costs of wasted materials and potential damage to the mixer and the tank.
Poly Processing can drill the holes for the mixer shafts at the factory if we have all of the details and the drawing details the hole sizes and locations.
We recommend contacting us before you begin the design of the tank mixing system so that we can help.
Learn more about the right mixing system for your chemical storage tank — download our complete product catalog today.
- October 14, 2024
- Topics: Fittings and Accessories
About Poly Processing
Posts By Topic
Tech Talk Podcast Episodes
Subscribe By Email
Recent Posts
- The Largest Crosslinked True Full Discharge Tanks Available: 15,500 IMFO and 15,000 Sloped Bottom IMFO
- Contained Bottom Discharge for Double-Wall Tank
- Join Us at WEFTEC 2025 Conference & Exhibition
- Effective Wastewater Treatment Chemical Storage
- How to Safely Store Sulfuric Acid to Overcome its Corrosive Nature
Tank Configurator
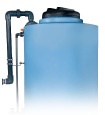
Find the recommended tank and system components for your chemical storage challenge.
Configure a Tank Package