Navigating the Various Types of Polyethylene
Just because different tanks are made from polyethylene, doesn’t mean they will give you the same performance. Various polyethylene tanks may not even be suitable for storing the type of chemical you use.
Polyethylene is available in several different types of resin. Some types are made for injection molding, others for extrusion, others for blow molding and yet others for rotational molding.
Beyond being designed for a specific manufacturing technique or process, the polyethylene resins also differ in density and structural strength. While strength of the wall differs greatly from type of resin, the chemical formula and chemical resistance remain largely unchanged. Let’s take a look at the types of polyethylene and their applications.
Common Types of Polyethylene
The most common types of polyethylene are high-density and low-density. When you think of the plastic you see in your everyday life — such as milk jugs, laundry detergent bottles, and plastic toys — those types of products are made of high-density polyethylene (HDPE).
This material can be used in tank manufacturing because it is a strong material with high chemical resistance.
HDPE is a thermoplastic material, which means it can be melted and reformed into something else. Unfortunately, that also means that HDPE tends to be notch sensitive. When under certain kinds of stress, these tanks can literally unzip in many different chemical storage applications. Poly Processing manufactures its line of water tanks out of HDPE, where the risk of unzipping is minimal.
Low-density polyethylene (LDPE), used in plastic bags, plastic wrap, and snap-on lids, is also highly chemical resistant and is a thermoplastic material. Linear low-density polyethylene (LLDPE) is a tougher substance and can be used in tank manufacturing. LLDPE has a narrower molecular weight distribution than LDPE.
Cross-Linked Polyethylene
Cross-linked polyethylene (XLPE) is made from high-density polyethylene (HDPE) that has an additive package compounded into it. This results in the polymer chains bonding together, making a polyethylene chemical storage tank a more robust product.
A standard HDPE tank can fail catastrophically, or unzip due to the polymer chains not being crosslinked together. XLPE is a much safer storage solution because the plastic cannot “unzip” — it’s a thermoset material.
The cross linking happens on a molecular level, so any failure happens at one of the millions of cross linked spots, minimizing the potential risk. Since XLPE is a thermoset plastic, there is significant improvement in the material’s mechanical properties, providing enhanced chemical resistance, heat resistance, structural integrity, and longer life.
Engineered Oxidation Resistant Tank Resin
Engineered oxidation resistant resin, also known as OR-1000™, is made of an inner layer of polyethylene that’s specifically formulated to resist oxidation. The outer tank surface is made of XLPE for superior strength. The two surfaces are molecularly bound together during the roto-molding process, creating a truly seamless bond between the XLPE and the OR-1000 resin system.
The OR-1000 system was specifically engineered to address the aggressive oxidation effects of sodium hypochlorite, sulfuric acid, hydrochloric acid, and other oxidizing chemicals. It is designed to maximize the useful life of storage tanks in oxidizing environments.
Here at Poly Processing, we are innovators of engineered high performance tank resins. We continue to develop polyethylene resins to give the end user superior strength and durability, as well as excellent chemical resistance.
To find out more about our XLPE tank offerings, talk to a chemical storage expert.
- April 18, 2022
- Topics: Value Added, Tank Design and Materials
About Poly Processing
Posts By Topic
Tech Talk Podcast Episodes
Subscribe By Email
Recent Posts
- Join Us at WEFTEC 2025 Conference & Exhibition
- Effective Wastewater Treatment Chemical Storage
- How to Safely Store Sulfuric Acid to Overcome its Corrosive Nature
- The Complete Journey of Owning and Retiring a Polyethylene Storage Tank
- Is Polyethylene a Storage Solution for Elevated Temperature Tanks?
Tank Configurator
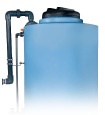
Find the recommended tank and system components for your chemical storage challenge.
Configure a Tank Package