A 5 Minute Overview of Chemical Storage Tanks
If you’re new to the chemical tank storage world, it’s likely that you have a lot of questions. Which type of tank is best? What materials are available? What materials are best equipped to handle the chemical you need to store? It’s helpful to know what is standard in the marketplace, the best options for your chemical, and what enhancements might be available to make your chemical storage selection easier.
Types of Chemical Storage Tanks
There are three different chemical storage tanks predominant in the market today: stainless steel tanks, fiberglass (FRP) tanks, and polyethylene tanks. Stainless steel tanks are durable and effective, but they are incompatible with many acids and your most expensive option. FRP tanks are viable options for some applications, but contain seams which can leak, handcrafted so more susceptible to human error, require increased maintenance, and are vulnerable to certain chemicals like hydrofluorosilicic acid, which is a chemical that actually etches glass. (the structural component of FRP)
Polyethylene storage tanks are available in both linear and cross-linked polyethylene and are easily the most versatile tanks on the market.
A Word About The Chemical You’re Storing
When you begin planning your chemical storage tank system, it’s crucial that you consider your chemical first and foremost. Many think that if a tank can store water, it can store a chemical. While that water tank might be able to store a chemical for a certain amount of time, it is not designed specifically for the chemical, so different factors can degrade the tank and cause leaks and other dangerous situations. Luckily, polyethylene storage tanks can be designed to handle any type of chemical you wish to store.
Different Types of Polyethylene Chemical Storage Tanks
Polyethylene tanks are strong, sturdy, affordable, and offer value in their longevity and the peace of mind you have in knowing that the tank is designed for your chemical’s particular application. Polyethylene tanks are created in a mold which eliminates the potential for human error. They also come in a variety of options that help protect your chemical, your storage environment and your employees.
-
Linear Polyethylene – differs from cross-linked polyethylene in that they are 10-20% less expensive, but they don’t offer the protection and durability of their cross-linked counterparts. Factoring in price per year the tank will last (life cycle cost), XLPE is actually far less expensive over time.
-
Cross-linked Polyethylene (XLPE) – is generally the best material for most chemical storage applications. It’s a robust material created with catalysts built into the polyethylene that bond polymers, creating unmatched tear-resistant strength for high performance chemical storage.It has the same molecular formula as other PE, so the same chemical compatability. The difference is only that XLPE bonds the PE chains together and significantly increases strength, longevity, and other engineering properties. These are quantified through many technical papers throughout the industry.
Enhancements to XLPE Storage Tanks
XLPE chemical storage tanks come in a variety of configurations that answer chemical storage pain points with innovative and long-term solutions. Because there are no seams or layers built into these tanks – they are one-piece homogenous containers – they offer superior storage and safety features. If we go back to the chemical you intend to store, it’s helpful to take a look at the behavior of certain chemicals and some cross-linked polyethylene tank options available to address that behavior.
A chemical that is highly oxidizing, like sulfuric acid, is difficult to store because oxidation degrades the tank and can cause dangerous exposure of the chemical. An antioxidant layer inside an XLPE tank can reduce oxidization fourfold – creating a safer environment for your chemical.
Chemical storage areas with space limitations can benefit from a cross-linked polyethylene tank-within-a-tank (or nested tanks) when there is no room for outside secondary containment. This type of tank actually provides 110% containment or more. Additionally, concrete secondary containment areas are not always safe, as some chemicals can eat through concrete.
A chemical that produces sludge, like a ferric, alum or polymer, or a chemical that produces fumes, like hydrochloric acid, present unique storage challenges. Sludge-producing chemicals require a tank that drains fully because the buildup can be dangerous in the tank. Fuming tanks need bottom full drainage so there is no need for a person to enter the tank for cleaning. A full-drain tank with the flange molded as low as possible, below the tank’s knuckle radius, is the best option. Furthermore, when the flange is part of the tank itself – molded into the original tank – it reduces the chance of leaks and spills.
For more information on tanks and fittings for your chemical storage system, download our full product catalog.
- April 7, 2015
- Topics: Tank Design and Materials
About Poly Processing
Posts By Topic
Tech Talk Podcast Episodes
Subscribe By Email
Recent Posts
- The Largest Crosslinked True Full Discharge Tanks Available: 15,500 IMFO and 15,000 Sloped Bottom IMFO
- Contained Bottom Discharge for Double-Wall Tank
- Join Us at WEFTEC 2025 Conference & Exhibition
- Effective Wastewater Treatment Chemical Storage
- How to Safely Store Sulfuric Acid to Overcome its Corrosive Nature
Tank Configurator
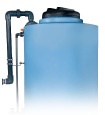
Find the recommended tank and system components for your chemical storage challenge.
Configure a Tank Package