Cross-Linked Polyethylene Tanks vs Extrusion Wound Tanks: What’s The Truth?
In this blog we look at two types of plastic tank manufacturing, rotational molding and extrusion winding and explain how each process works and the benefits of a seamless (homogenous) tank for chemical storage.
In polyethylene chemical storage tank manufacturing, there are a couple of popular processes to produce tanks. One involves rotationally molded tanks and the other is extrusion wound tanks. Each of these types of tanks are manufactured in a specific way. For some applications, the process by which a tank is manufactured is critical.
Let's look at both types, how they're made, and the differences between the two products.
What is an Extrusion Wound Tank?
An extrusion wound tank is a multi-seam, wound, polyethylene tank. In this process, the polyethylene varies in thickness depending on the size of the tank and the specific gravity of the material it will hold. It is wound around a mandrel and as that happens, the polyethylene sheet is melting against itself to create the storage tank. This process started in plastic pipe manufacturing many years ago and is still used today.
In this type of multi-seam system, connectivity occurs as the strands melt together as it rotates around the mold. In many ways, it is a welded tank and can have hundreds of feet of seams in the sidewall of the tank.
Issues With Extrusion Wound Tanks
The fact that extrusion wound tanks have these seams is problematic for many chemical applications since most tank failures will happen at the seams or weaker areas.
Extruded polyethylene will not leak at the sheet level in most cases unless it is chemically attacked or becomes brittle due to UV degradation. Instead, leaks start at the seams. Even though the manufacturing process is semi-automated, there is still a concern for the quality of those seams over time.
In a similar fashion, since the body of the tank is wound on a mandrel, the top and bottom, and all of the fittings have to be hand welded onto the body after the main winding is completed. That presents another challenge: the tank has a wound sidewall with hand welded fittings as well as a hand welded top and bottom. That opens up the potential for manufacturing defects and possible leaks in all areas due to all of the welding.
XLPE Tanks Are Stronger and More Secure
The great thing about XLPE manufactured tanks is that there are no seams. The polyethylene is a one piece, seamless, homogenous unit because it is rotationally-molded.
Rotational molding involves a heated hollow mold which is filled with a charge or shot weight of material. It is then slowly rotated (usually around two perpendicular axes) causing the softened material to disperse and stick to the walls of the mold. In order to maintain even thickness throughout the part, the mold continues to rotate at all times during the heating phase and to avoid sagging or deformation also during the cooling phase.
Thickness of the tank with rotational molding is maximized at the tank sidewalls and bottom knuckle radius. This creates extra strength where it’s needed. The lower sidewalls and bottom knuckle radius are engineered to handle the hoop stress that is placed on the tank due to the weight of the chemical being stored.
There's no welding and no worries about failures at the seams. The polyethylene is molded as a monolithic part and the end result is a one piece product without seams, weldments, or breaks in the sidewall.
Poly Processing has been manufacturing crosslinked polyethylene tanks for over 40 years using the rotational molding process. Poly Processing manufactures rotationally molded vessels in three locations located across the United States. Monroe, Louisiana. French Camp, California. Winchester, Virginia. The nine rotational molding machines can manufacture vessels from 30 gallons up to 14,000 gallons and tanks as large as 14 feet in diameter by 18 feet tall. Custom sizes and shapes to fit your unique storage requirements are available as well.
Poly Processing Company designs and builds tanks to the ASTM-D1998 standard. There is no U.S. standard that we are aware of for extrusion wound tanks.
Let us engineer your tank solution for you.
To learn more about XLPE and the advantages it has over extrusion-wound tanks, contact Poly Processing today.
- May 18, 2016
- Topics: Tank Design and Materials
About Poly Processing
Posts By Topic
Tech Talk Podcast Episodes
Subscribe By Email
Recent Posts
- Join Us at WEFTEC 2025 Conference & Exhibition
- Effective Wastewater Treatment Chemical Storage
- How to Safely Store Sulfuric Acid to Overcome its Corrosive Nature
- The Complete Journey of Owning and Retiring a Polyethylene Storage Tank
- Is Polyethylene a Storage Solution for Elevated Temperature Tanks?
Tank Configurator
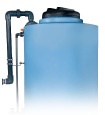
Find the recommended tank and system components for your chemical storage challenge.
Configure a Tank Package