Crosslinked Polyethylene Storage Solutions For Your Industry: Part 1
Poly Processing tanks are used for water and wastewater treatment applications, but are also found in dozens of industries nationwide. We’re able to work with a wide variety of businesses and organizations that use chemicals to produce goods and products.
This is the first in a series of articles over the next several months that will feature a selection of the markets we serve. (View the full list of the markets we serve.)
In this article, we highlight these four industries that Poly Processing provides solutions for:
- Agriculture
- Beer and Wine
- Brine
- Clean-in-place
Agriculture
Due to their superior physical properties, Poly Processing’s tanks are frequently used in the agricultural industry. Our industry leading tanks are used to store and transport liquid fertilizer chemicals, water, and other agricultural chemicals such as pest control applications. Poly horizontal tanks are a popular product, because they provide three valuable benefits:
- Cross-linked polyethylene horizontal storage tanks are lightweight yet incredibly robust and impact-resistant, which is especially ideal if you’re moving the tank often.
- Horizontal tanks eliminate concerns about height restrictions in confined spaces.
- Horizontal tanks are most often the preferred choice for smaller applicator tanks because they are transported often.
Horizontal tanks tend to be smaller tanks, which means that they can be mounted and moved easily. In the agricultural world, you can find horizontal tanks mounted on trailers, skids, trucks, or tractors for transportation to the site where the application is required. In addition, they might be mounted on specialty equipment in the field or at a facility.
Beer and Wine
Traditionally, breweries use stainless steel for all components of beer making, including wastewater treatment and storing raw materials. While steel tanks are best for pressurized or elevated temperature situations, tanks that are manufactured using crosslinked polyethylene (XLPE) are a good choice pre- and post-production.
Why are breweries and wineries choosing polyethylene storage tanks pre- and post-production?
- Cost-effectiveness. On average, polyethylene tanks cost 80% less than comparable stainless steel tanks.
- Portability. Plastic tanks are lighter and easier to move. If you plan to scale, XLPE tanks won’t get in your way or slow you down. Cross-linked polyethylene tanks are an ideal solution for transporting grapes in gondolas.
- Rapid delivery. Polyethylene tanks can usually be ordered and delivered within 8-10 weeks. If you order a stainless steel tank, you could be waiting for several months.
- Scalability. Polyethylene tanks are available in a variety of sizes, from 30-gallon to 15,500-gallon tanks. As your business grows, you can easily order the next size tank you need and have it quickly delivered. Lower overhead, lower costs, superior tank life, and quicker delivery fit a cost-effective business model.
While Poly Processing’s core business is chemical storage, we apply the same stringent demands for quality construction and fittings to our beer and wine tanks. Our optional airtight lids and standard thick durable tank walls give you a cost-effective aging wine tank storage solution for unoaked chardonnay and red wines. After production, they’re a reliable solution for wastewater treatment.
For more information on storing wine, and storage tank recommendations, download our Wine Storage System Guide.
Brine Storage
Sodium chloride brine results from the conversion of salt and water into “saturated brine.” To make-up and properly store brine, you must have a properly designed vessel which incorporates the features necessary to prevent freezing, provide sufficient venting capacity, capture salt dust, relieve excessive pressure, and maintain sufficient levels of water so that the brine being supplied to your process is fully saturated.
Compared to other storage options, cross-linked polyethylene (XLPE) storage tanks are more cost effective, offer fast production time, come with a longer warranty, and are less prone to damage.
Poly Processing tanks rise to all the challenges of brine make-up and storage.
- Proper ventilation — Salt dust can be extremely damaging to surrounding equipment and materials. XLPE briners from BrineMaker, Inc. include dust bags designed to capture the corrosive salt dust while allowing the briner to “breathe”.
- Level Control — Maintaining the proper water level within the tank to produce the required brine solution is critical. An electronic sensor monitors the water/brine level and an automated water inlet valve controls the liquid level at predetermined points.
- Access for tank cleaning — BrineMaker, Inc. has standardized on side manways for all pneumatically loaded designs to provide safe and simple access for internals inspection, maintenance, and cleanout.
- Freeze Protection — A Heat-Loss Prevention System of heating pads, insulation, and a controller maintains the ambient temperature of the brine solution in cooler climates.
Poly Processing Company works with BrineMaker, Inc., the leading supplier of brine make-up and storage solutions. BrineMaker, Inc. has standardized on crosslinked polyethylene tanks by Poly Processing and offers a comprehensive menu of options for turnkey design and supply. Contact us if you’re interested in learning more.
Cleaning Agents/Clean-in-Place
Clean-in-place (CIP) systems are becoming more and more popular in the food manufacturing industry. Detergents and surfactants, like caustic soda, are particularly corrosive and Poly Processing company understands this. We design our crosslinked tanks with the chemical to be stored. A XLPE tank helps extend the life of the tank and in most cases avoids cracking and breakdown of tank materials that could lead to a potential leak. Crosslinked tanks are inherently stronger, with greater tensile strength and advanced stress crack resistance, and they withstand the damaging effects of surfactants.
Poly Processing offers several storage solutions that are ideal for storing CIP chemicals:
Full-discharge IMFO Tank®. The IMFO Tank is a true, 100 percent full-drain tank, because the outlet flange is molded below the two-inch knuckle radius. No other vertical tank features an outlet flange below the knuckle radius. With the IMFO, the outlet flange is guaranteed leak-free, because it’s molded into the wall, not attached after production.
OR-1000™ System. Storing ultra-high purity cleaning chemicals often requires an interior surface that resists bacteria growth. Poly Processing’s OR-1000 System adds an antioxidizing interior barrier between the chemical and the crosslinked polyethylene. The OR-1000 system is bonded to the crosslinked polyethylene during the manufacturing process, creating a seamless, covalent bond that will last the entire life of the tank. The OR-1000 system is all about extending the life of the tank and giving the user greater useful life.
SAFE-Tank®. The SAFE-Tank is a tank-within-a-tank (or double-wall) tank that allows you to keep an acid tank and a base tank in the same area without the risk of contamination. Any leaking or spilling is safely contained within an interstitial area of the double wall.
Bellows Transition Fitting. When you install a SAFE-Tank with a sidewall fitting, it may be important to also install a Bellows Transition Fitting. The Bellows Fitting lets you safely connect the primary tank with a secondary containment tank. For even greater protection, tank pipes can be contained with a custom transition fitting and containment piping to contain leaks. This containment option can be clear, so that you can see the condition of the pipe or spot chemical leaks.
Have questions about polyethylene storage tanks in one of these industries? Contact a chemical storage tank specialist today.
- May 8, 2023
- Topics: Applications, Tank Design and Materials, Chemical Storage
About Poly Processing
Posts By Topic
Tech Talk Podcast Episodes
Subscribe By Email
Recent Posts
Tank Configurator
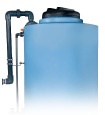
Find the recommended tank and system components for your chemical storage challenge.
Configure a Tank Package