[Featured in ES&E Magazine] Creating a Safe Chemical Storage System
Whether you’re an engineer writing a spec for a chemical storage system, or an end user who is looking for the best way to store corrosive chemicals, there are multiple factors that go into creating a safe storage system. Cost might be your first consideration, but there is more to consider than the initial price of the tank, its fittings and accessories, delivery, installation and tank longevity.
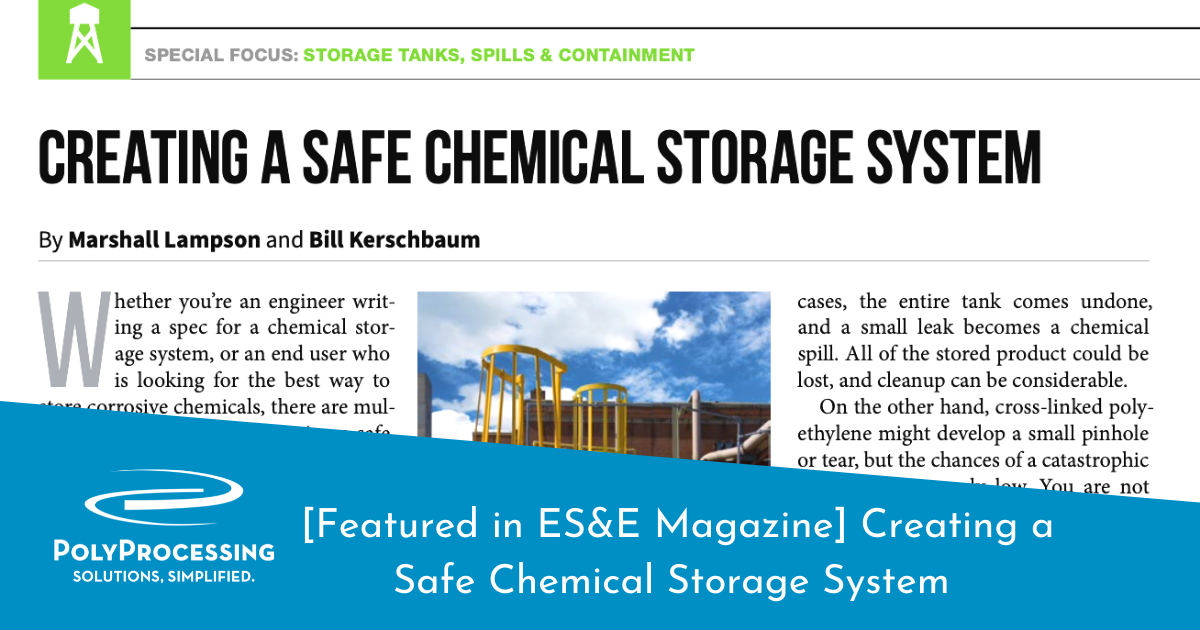
This article was originally published in ESE Magazine in June, 2021.
Manufacturing Update
We know that delivery times are critical to our customers. That's why we are working diligently to ship every order within 5-7 weeks. FRP tank manufacturers and many poly tank manufacturers are giving their customers a 22-36 week plus shipping window based on lack of raw material sourcing, Covid-19, etc. At Poly Processing Company we deliver your product in one fourth of the time.
Before you order an FRP tank, make sure the manufacturer gives you the price and leadtime up front. If you don't get price and leadtime up front, you could be in for a rude awakening.
Trusted, consistent, and expeditious, Poly Processing’s rotationally molded crosslinked tanks are by far the toughest polyethylene tanks offered to the chemical market. With our 5-7 week delivery window, we strive to deliver peace of mind and an ease of business to each and every customer. Call us at 866-765-9957 and let us help you, we understand response time!
It is important to consider the durability and longevity of the tank system when you’re storing corrosive chemicals. In fact, every good tank design starts by considering the chemical you’re storing. Everything else flows out of that. Leaks and degradation can be costly to repair. It is even more costly when a tank system has to be replaced because it wasn’t engineered to store the right materials.
Which Chemicals Are Corrosive?
A corrosive chemical is one that will damage or destroy another substance upon contact. In most cases, the higher the concentration, the more corrosive it is. It can cause chemical burns to live tissue, and the chemical fumes can cause eye and lung irritation or damage. Both acids and bases can be corrosive. Some commonly stored corrosive chemicals include peracetic acid, sulfuric acid, hydrochloric acid, sodium hypochlorite, nitric acid and sodium hydroxide.
Many of these chemicals can corrode metal, especially at higher temperatures. When metals corrode because of these substances, they often give off a hydrogen gas, which is flammable.
If you are storing chemicals in a plastic tank, there is little to no metal to corrode and you are protected from these hazardous fumes. Polyethylene is a durable plastic that is available in many types including medium-density, high-density (HDPE) and high-density cross-linked (XLPE) forms. Medium- and high-density polyethylene are usually linear, which means that the polymers of the plastic are joined in a twisted formation like rope fibres, rather than knotted in nature.
XLPE is created in a way that the very molecules of the plastic are bonded and linked. Imagine a chain link fence where the metal is actually linked together. These factors mean chemical resistance, heat resistance and dimensional stability are very high.
Cross-linked polyethylene has covalent bonds that connect its polymer chains. These bonds tie the polymers together and lengthen the polymer chains, giving the polyethylene stronger resistance to impact and a longer life. The molecular structure provides stress cracking resistance, improved toughness, and in many cases much greater useful life.
The implications of these differences are most obvious when testing plastics. When linear polyethylene fails, it can fail catastrophically, because the linear polymer chains tend to “unzip.” In some cases, the entire tank comes undone, and a small leak becomes a chemical spill. All of the stored product could be lost, and cleanup can be considerable.
On the other hand, cross-linked polyethylene might develop a small pinhole or tear, but the chances of a catastrophic failure are extremely low. You are not likely to lose all of the stored chemical if a leak develops, and the cost of cleanup and replacement in most cases is significantly less. As well, the risk to employees and the environment can be drastically reduced. In most cases, cross-linked polyethylene offers much longer useful life in the same application as linear polyethylene.
Based upon feedback from customers over the last 45 years, the typical useful life of storage tanks made from XLPE is 15-20 years or greater. However, there are factors that impact this lifespan.
The types of chemicals stored, the concentrations of the chemicals, the filling frequency, and the operating temperature within the storage tank, all impact the useful life of a polyethylene storage tank.
For example, a high concentration of sulfuric acid (an aggressive stress cracking agent) will break down a tank quicker than 25% caustic soda. Or 12% sodium hypochlorite will degrade from UV exposure and elevated temperatures. As the breakdown of the chemical occurs, sludge builds up in the bottom of the tank, resulting in a potentially shorter tank life.
There are several innovations available to address these two chemical storage situations. The first is the antioxidant resin systems designed to slow the aggressive breakdown from storing sulfuric acid.
Another innovation is an Integrally Molded Flanged Outlet®, or IMFO® System. This system, with the flange molded into the bottom of the tank, permits full discharge of the tank. Sludge buildup from storing chemicals, such as sodium hypochlorite, can be easily removed without a confined space entry, extending the useful life of the tank and keeping employees safer.
Improper installation and “hard” piping are the greatest factors reducing useful tank life. Polyethylene is inherently able to expand and contract and can safely store a broad spectrum of chemicals. Proper flexible connections accommodate this tank expansion, leading to extended life of the tank.
While often overlooked, proper venting plays an important role in extending tank useful life. Since polyethylene tanks are rated at atmospheric pressure, or vacuum, adequate vent size is important to accommodate flow and delivery rates. Factors to consider in determining proper venting include:
- Will the tank be filled pneumatically or mechanically?
- Is the tank vented to the outside atmosphere?
- Is the vent length longer than 3 feet?
- Is fume scrubbing used?
- Are there vent screens that restrict flow?
- Are emergency venting specs provided by the manufacturer?
Three additional factors that determine storage tank useful life are continuous cycling (filling and discharge), excessive agitation in mixing and mobile applications.
To extend tank longevity, you can store corrosive oxidizing chemicals in an XLPE tank with an antioxidant barrier system. The technology behind true antioxidant barrier systems takes the guesswork out of choosing the right storage tank system for oxidizing chemicals.
Antioxidant additives are used to extend tank life. This fights off corrosion caused by oxidizing chemicals, regardless of the type of plastic. Antioxidants extend the longevity of HDPE, XLPE, nylon, and any other plastic, since they are all carbon based. Oxidation slowly deteriorates any carbon based bond, whether it is in a plastic, plant, or animal.
One company uses a resin system made of polyethylene, but what makes it special is the 400% more antioxidant additives in that resin. It is added to the chemical tank during the roto molding process, which creates a seamless bond between the barrier resin and the XLPE polyethylene. This unique combination of polyethylene creates an ideal containment for even the most corrosive chemicals. XLPE gives you the strength and tank longevity, while antioxidant resins give you optional additive oxidation resistance over time.
The Best Business Decision for Chemical Storage
There is a significant cost to installing and replacing a chemical storage tank. Many companies only calculate the tank purchase cost and shipping costs when deciding to purchase a new tank or replace an existing one. However, there are several additional factors to consider as well.
If you need the chemical on a daily basis, you might bring in a smaller temporary tank while the new one is being manufactured and shipped. In many cases we recommend purchasing a backup storage tank as well, to ensure that you have redundancy and do not run out of chemicals. Getting the old tank out of the building can be a large undertaking. A crew will need to disconnect the piping, pumps and other accessories. The tank will need to be pulled out of the building, or, if it is too large to pull through the doors, it will need to be cut up and removed.
If the new tank is too large to maneuver through the entrance, you may need to remove the paneling or roofing, and lift the new tank inside the building with a crane. Also, the time and labour involved with plumbing can be very costly.
Whether you purchase a cheap tank or an expensive tank, it is important to install the best chemical storage system for the greatest useful life. While XLPE tanks can have a slightly higher upfront cost, the investment means fewer maintenance costs and greater savings.
Call us at 866-765-9957 and let us help you, we understand response time!
- July 19, 2021
- Topics: Fittings and Accessories
About Poly Processing
Posts By Topic
Tech Talk Podcast Episodes
Subscribe By Email
Recent Posts
- The Complete Journey of Owning and Retiring a Polyethylene Storage Tank
- Is Polyethylene a Storage Solution for Elevated Temperature Tanks?
- The Economics of Chemical Storage: How to Maximize ROI on Your Tank Investment
- Lids for Fume-Tight Tanks: What Are My Options?
- Insulating Your Chemical Storage Tank: Why It Matters and How to Do It
Tank Configurator
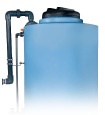
Find the recommended tank and system components for your chemical storage challenge.
Configure a Tank Package