Lessons from the West Virginia Chemical Spill: Safe Chemical Storage Is No Accident
On January 9,2014, a chemical spill fouled the water supply for thousands of West Virginians. "Crude MCHM," 4-methylcyclohexane methanol used in washing coal and removing impurities, leaked from the Freedom Industries facility into the Elk River near Charleston, WV. In addition to the leak at the Freedom Industries’ chemical storage facility, Freedom Industries has since been cited for unsafe storage conditions at a second chemical storage site. Freedom Industries has subsequently filed for bankruptcy.
Let’s examine the factors contributing to the Elk River spill.
Improper Chemical Storage Procedures, Lack of Effective Secondary Containment, No Documented Tank Inspections Spell Disaster
The spill began on January 9, 2014 when up to 7,500 US gallons of crude MCHM leaked from a one-inch hole in the bottom of a stainless steel storage tank and its containment area at Freedom Industries' Charleston facility.
From this incident, obvious safe chemical storage practices are found lacking and questions arise.
- Was stainless steel the proper material to store Crude MCHM? Was the tank properly equipped with leak detection?
- Secondary containment failed to confine the tank leak, resulting in the chemical entering the water supply. Either the secondary containment was inadequate in size and design to contain the tank leak, or it was improperly maintained. Large vessel secondary containment, or a SAFE-Tank® is a “tank-within-a-tank” system, designed to protect against catastrophic spills from a tank leak.
- Lack of documented tank and secondary containment inspections. It appears, that inspections of the chemical storage tank were lax or nonexistent. An annual chemical storage tank inspection helps to spot potential leaks and problems.
In addition to annual tank inspections, proper tank setup and installation, and routine tank maintenance play an essential role in safe chemical storage.
Finally, it’s smart to educate employees in the proper protocols to respond rapidly and effectively when a tank leak or chemical spill occurs.
The Elk River spill clearly shows that proper and safe chemical storage is no accident. Safe chemical storage begins with the right chemical tank storage system design. It includes secondary containment, proper leak detection, proper primary tank design based on the chemical being stored, etc. Safe chemical storage is even more important if chemicals can potentially enter the water supply or cause harm to personnel. Regular, documented tank inspections and routine tank maintenance spot potential leaks and problems early before a disaster happens.
If the Elk River spill raises safe tank storage questions in your mind, contact a Poly Processing tank specialist.
- January 21, 2014
- Topics: News and Customer Stories
About Poly Processing
Posts By Topic
Tech Talk Podcast Episodes
Subscribe By Email
Recent Posts
- Join Us at WEFTEC 2025 Conference & Exhibition
- Effective Wastewater Treatment Chemical Storage
- How to Safely Store Sulfuric Acid to Overcome its Corrosive Nature
- The Complete Journey of Owning and Retiring a Polyethylene Storage Tank
- Is Polyethylene a Storage Solution for Elevated Temperature Tanks?
Tank Configurator
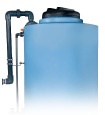
Find the recommended tank and system components for your chemical storage challenge.
Configure a Tank Package