Using A Nitrogen Blanket on a Poly Processing Tank
Water and oxygen can degrade some chemicals, so it may be necessary to create a protective barrier that keeps air and water moisture away from the chemical you’re storing. A nitrogen blanket can help increase the life of your chemicals.
Tank blanketing, or tank padding, describes the process of applying an inert gas to the vapor space (or unused space) that exists above the chemical inside a storage tank. Tank blanketing is mainly used to add a layer of gas (usually nitrogen) to keep air or moisture from a chemical inside the tank.
The Benefits of Tank Blanketing
Reducing the amount of oxygen in the vapor space of a chemical storage tank reduces the risk of any sort of fire and explosion when storing combustible chemicals, since air is needed for fire to burn.
Oxygen and moisture can corrode the tank when they react with the tank’s contents, as well. Certain materials, like food-grade chemicals and pharmaceuticals, are susceptible to degradation when exposed to O2 and H20, so blanketing protects them and keeps them from spoiling. Edible oils, for example, can be spoiled by reactions with air which compromises the oil’s stability. When edible oils are exposed to water, a chemical reaction occurs that permanently alters the oil’s properties.
Why Use a Nitrogen Blanket?
Nitrogen is an inert gas, which means that it does not react with most substances. It is widely available and less expensive than other gasses, like argon, which can be ten times as expensive as nitrogen. Carbon dioxide is used in some cases, but it’s a more reactive gas than nitrogen.
Design Requirements for Tank Blanketing
A few considerations must be factored in when designing cross-linked polyethylene tanks for tank blanketing. First, the tank must have a pressure relief valve. The valve must be set to a pressure that’s high enough to prevent oxygen from entering the tank, yet low enough to vent out nitrogen if the pressure within the tank is too high.
Cylindrical polyethylene storage tanks should never exceed a 6-inch water column or .36 psi, or else you risk losing your stored contents. Poly Processing’s engineering team can assist with the proper relief valves for your system.
When using inert gasses such as nitrogen, strict protocols must be followed to ensure that workers are not exposed to harmful or lethal doses of any non-breathable substances. Additionally, in the United States, OSHA regulates any commercial use of tank blanketing. Here are a few safety guidelines to keep in mind when using a nitrogen blanket system in a polyethylene tank:
- Ensure adequate ventilation: Nitrogen is a gas that can displace oxygen and create an oxygen-deficient atmosphere. Ensure the area has proper ventilation and that the tank is placed in a well-ventilated location.
- Only use food-grade nitrogen: The nitrogen used to blanket the tank should be food-grade quality. It should be free of impurities to prevent contamination of the stored product.
- Keep the tank sealed: Once the nitrogen blanket is in place, the tank should be sealed. This will prevent any air or other gas from entering the tank and contaminating the stored product.
- Monitor the oxygen level: It's important to monitor the oxygen levels in the area where the tank is located. This is usually done with an oxygen sensor, which alerts you if the oxygen level in the area falls below a safe level.
- Properly dispose of nitrogen: Nitrogen should be vented into a safe area, and should not be released near the tank or in any area where people may be present.
The Best Tank Systems for Tank Blanketing
Cross-linked polyethylene (XLPE) tanks are a better option for tank blanketing than other chemical storage systems, such as stainless steel or fiberglass reinforced plastic (FRP). Polyethylene can last longer than other materials, and it’s more cost-effective.
Stainless steel is often considered a standard for the food industry, but it’s also very expensive. FRP, on the other hand, is not nearly as robust as XLPE, which has a broader range of chemical compatibility.
Sloped Bottom IMFO Tank Excels for Glues and Adhesive Companies
Liquid glues, or white glues, are water-based adhesives that are used in a wide variety of applications. They’re popular, because they are eco-friendly, non-toxic, easily recyclable, and safe to handle. Many of these adhesives and glues require a nitrogen blanket to reduce the amount of oxygen in the headspace of the tank. Less oxygen means less glue that could be oxidized.
Most liquid glues don’t need to be heated before application and they clean up easily with water. These versatile adhesives have many uses, including packaging. Many of our customers that store liquid glues are cardboard box manufacturers. They trust Poly Processing because they know that our cross-linked polyethylene (XLPE) tanks provide an ideal storage solution for glue and provide greater life with nitrogen blanketing systems.
Poly Processing’s sloped-bottom IMFO tank is an ideal solution for heavier materials such as glues and adhesives. The gravity feed allows these heavier substances to discharge more easily, preventing sediment or sludge buildup.
It also makes tank maintenance and cleaning easier. There’s no need for a confined-space entry, and no need to get in with a mop or pressure washer. The sloped-bottom IMFO tank can be cleaned from the top manway, or with a spray ball installed in the dome.
Choose a tank blanketing storage solution that’s affordable and lasts for years. Contact us today to discuss XLPE tank blanketing.
- August 7, 2023
- Topics: Applications
About Poly Processing
Posts By Topic
Tech Talk Podcast Episodes
Subscribe By Email
Recent Posts
Tank Configurator
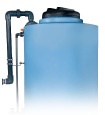
Find the recommended tank and system components for your chemical storage challenge.
Configure a Tank Package