For Full Discharge, Don’t Rely on Cone Bottom Tanks
When it comes to a full discharge tank, cone-bottom tanks get the job done—except when they don’t. The fact is, cone-bottom tanks fall short on several fronts.
Cleaning cone-bottom polyethylene tanks can be challenging. They require additional vertical space and safety precautions. And the tanks themselves cost a pretty penny — especially when you have to include a stand and basket to support the cone-bottom tank. Prices can skyrocket in today's market with the costs of metal and special coatings. Lead times for welded steel products can be extremely long as well.
Draining the tank is sometimes easier said than done. Space constraints, incorrect fitting placements, and dealing with hazardous chemicals can make routine maintenance complicated.
It can be tempting to put off regular tank draining, inspection, and maintenance, but that can be a dangerous option. Delayed maintenance could harm your chemicals, your equipment, and possibly even your employees. It can also result in unexpected financial costs for your company.
A better option is full-tank discharge. Full-tank discharge makes it easier to clean and maintain your chemical storage system in the following ways:
- Minimizing residual chemicals. Full-discharge tanks help eliminate remnants of older chemicals that are left behind, preventing contamination of the new batch of chemicals.
- Easier and safer tank cleaning. A proper full-drain system means plant employees don’t need to enter a tank and risk contact with hazardous chemicals in the confined space.
- Eliminating free radicals. When certain chemicals are stored over time, salts and metals fall out of the chemical and collect at the bottom of the tank. If you don’t have full-tank discharge, new chemicals that are placed in your tank will mix with the salts and heavy metals, creating free radicals. These free radicals attack the interior surface of the tank, which can compromise the integrity of your chemical storage tank.
- Preserving structural integrity. With full-discharge systems, you don’t need to drill holes in the tank to add side-manways or fittings. Drilling holes creates an opportunity for structural damage, and potential for deterioration of gaskets and fittings. Everything can be handled from the outside of the tank.
Not All Full-Discharge Tanks Are Created Equal
To construct a full-discharge system, some companies manufacture tanks out of one substance and insert a metallic fitting in the mold or install a fitting after production. It’s a common and much less expensive solution in the chemical tank manufacturng industry, but this method creates new problems. These problems include compromised structural integrity, tank maintenance issues, gasket and O-ring failures, and less than full discharge issues.
Compromised Structural Integrity
An insert, whether it’s molded in or installed post-production, can impact the tank’s hoop integrity. This puts the entire plastic storage tank at risk of structural stress from volatile chemicals.
Inserts are metallic and don’t have the same chemical resistance as the plastic tank itself. So chemical reactions where the tank meets the metal can create a stress point for the plastic itself. Before long, it can create leaks or cracks in the tank wall.
Tank Maintenance and Draining Issues
Inserts need to be installed one to two inches above the knuckle radius of the tank. A couple inches makes a big difference, because that means you’ve got two inches of chemical or sediment sitting in the bottom of the tank. Your full-drain system isn’t actually full-drain, and it still requires manual clean-out—a dangerous and time-consuming process.
There’s also the fact that inserts aren’t the same material as the tank. Most inserts are metallic and the tanks are plastic, which creates a difference in expansion and contraction coefficients. That difference can cause problems in the future.
A Better Full-Discharge Solution
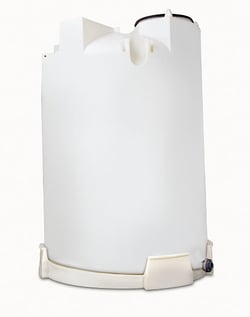
Poly Processing offers a better polyethylene full-discharge solution that eliminates many of the problems that other full-discharge systems don’t fix. Our innovative Sloped-Bottom Integrally Molded Flanged Outlet® (IMFO®) System features a flange that’s molded at the very bottom of the tank’s sidewall, below the knuckle radius—not two inches above it.
Sloped-bottom IMFO tanks and our vertical tanks with IMFO are the only full-discharge polyethylene tanks to provide a true molded-in full drain of your stored chemicals.
The Sloped-Bottom IMFO is a rotationally molded high-density cross-linked plastic tank. It is one single piece with no seams. The IMFO flange is molded as part of the tank during manufacturing, rather than being introduced post-production as an insert. The floor of the tank is sloped towards the IMFO flange, giving you the greatest possible complete drainage system in a vertical tank design.
Because the slope and the flanged outlet are molded as part of the tank, there are no fittings and no risk of leaks or stress cracking. The one-piece construction also enhances the tank's long-term performance since it doesn’t compromise the tank hoop’s integrity or structural design.
Any required maintenance is simple and hassle-free, as the flange extends away from the tank wall. The entire flange system is external to the tank, with easy hardware access from outside the tank—unlike metallic inserts.
Sloped-bottom IMFO for Heavier Chemicals and Substances
The Sloped-bottom IMFO tank excels when it comes to discharging heavier materials such as FOG (fat, oils, and grease) or sludge like materials. The additional gravity feed makes it easy for heavier substances to discharge completely, leaving no residue or sludge to build up.
Cleaning is simple, because there is no need for a confined-space entry. Instead, the sloped-bottom tank can be cleaned from the top manway, or with a spray ball installed in the dome. It’s a solution that’s much safer for your personnel, and more cost-effective.
Poly Processing Company has hundreds of Sloped-bottom IMFO Tanks installed in a variety of applications, including:
- Water and wastewater treatment
- Industrial applications
- Fats, oils, and grease storage
- Food and beverage
And many more.
Get the Full-Discharge System You Need
If you need a full-discharge tank, make sure you’re truly getting 100 percent full-discharge. And make sure you purchase a tank that can give you the structural integrity and longer useful life.
Learn more about full-discharge systems — download the Sloped-Bottom IMFO Tank Guide.
- May 1, 2023
- Topics: Tank Design and Materials
About Poly Processing
Posts By Topic
Tech Talk Podcast Episodes
Subscribe By Email
Recent Posts
Tank Configurator
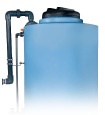
Find the recommended tank and system components for your chemical storage challenge.
Configure a Tank Package