The Next-Generation System for Oxidizing and Corrosive Chemical Storage
One of the challenges in storing any oxidizing chemical is engineering a chemical storage tank that not only contains the chemical but has a greater useful life and measure of safety. Whether you’re storing sodium hypochlorite, sulfuric acid, hydrochloric acid, or other oxidizing substances, it is critical to design the storage tank with the chemical in mind.
Poly Processing Company (PPC) has been a leader in rotationally molded crosslinked polyethylene (XLPE) storage tanks for 50+ years. PPC works with leading universities and chemical manufacturers and suppliers to develop engineered polymer systems that perform above and beyond any standard off-the-shelf polyethylene tanks — especially in harsh, oxidizing environments.
One of the chemical storage innovations we’ve developed is the OR-1000™ system. This engineered system is the result of an initiative aimed at defining and addressing the long-term failure mechanisms associated with polyethylene when storing strong oxidizers and other corrosive chemicals.
The OR-1000 system consists of engineered resins for oxidizing applications to provide superior environmental stress cracking resistance (ESCR).
What is the OR-1000 system?
The OR-1000 system is an engineered resin with four times the antioxidant power of a standard tank wall. Poly Processing’s exclusive OR-1000 system was specifically designed to address the aggressive oxidation effects of hazardous chemicals such as sodium hypochlorite, sulfuric acid, and hydrochloric acid. It does this by adding an additional resin system between the XLPE and the chemical.
The OR-1000 is designed to maximize the useful life of chemical storage tanks in oxidizing and corrosive environments. This system greatly increases the life of a crosslinked polyethylene tank, giving you a much more cost-effective solution.
OR-1000’s engineered resin system is made of polyethylene that is specifically formulated to resist oxidation by corrosive chemicals. Its outer surface is made of XLPE for superior strength. Its inner and outer surfaces are molecularly bound together during the roto-molding process, creating a truly seamless bond between the XLPE and OR-1000 system.
Long Term Improvements
The OR-1000 system’s resistance to oxidative degradation is illustrated in the chart below. This chart compares the tensile elongation of the OR-1000 system and two different commercial rotational molding polyethylenes when exposed to 12.5% sodium hypochlorite (industrial strength bleach) solution at 40 degC. Sodium hypochlorite is one of the strongest corrosive chemicals that oxidizes polyethylenes.
After nine months of exposure to sodium hypochlorite, the conventional polyethylene tanks have lost an average of 30% of the original tensile elongation to break. During that time, the OR-1000 has lost only about 3%. This indicates that the OR-1000 has about 10X greater resistance to oxidative degradation.
Loss of elongation in this manner indicates an increasingly brittle tank or liner — and thus a greater susceptibility to cracking and leaking over time.
The data clearly demonstrates the superior long-term performance of the OR-1000 system for storing strong oxidizing chemicals such as sodium hypochlorite.
Environmental Stress Crack Resistance (ESCR)
Polymers such as polyethylene are especially susceptible to another type of failure known as environmental stress cracking (ESC). Stress cracking occurs when polymer chains start breaking in stressed areas of a tank. Examples of stress include normal heating and cooling of storage tanks in outside environments or pressurized filling and emptying of transfer tanks used in chemical manufacturing.
The stress cracking process is accelerated by storing solutions of hazardous chemicals, particularly dilute solutions in which the chemicals have increased mobility and can physically penetrate the polymer structure and increase the stress differences.
The chart to the right shows the difference of ESCR in tanks with and without OR-1000™.
Real World Benefits of the New OR-1000™ System
The OR-1000 system has an impressive track record with our customers, providing these real-world benefits:
- Improvements in the long-term properties: The enhanced resin lasts longer and allows your tank to last longer as well.
- High levels of Environmental Stress Crack Resistance (ESCR): High levels of resistance to environmental stress cracking in the presence of Sodium Hypochlorite, Sulfuric Acid, and other aggressive chemicals.
- Improved Elongation: The OR-1000 system maintains its elongation properties over time while in the presence of heavy oxidizing chemicals. This performance is superior to other HDPE materials used in tank construction.
- NSF/ANSI 61 – Poly Processing Company XLPE tanks with the OR-1000 system are NSF certified for 35 different chemicals.
To learn more about the Next Generation OR-1000 system, contact us.
Industry News
For over five decades, Poly Processing has been at the forefront of innovation in chemical storage tank design and manufacturing. Reinforcing our commitment to advancing crosslinked polyethylene (XLPE) tank technology, we are thrilled to unveil our latest update to our storage tank solutions: the 15,500-gallon IMFO tank, the 15,000-gallon Sloped Bottom IMFO tank, and the 15,500-gallon Vertical tank, are all available in specific gravities up to 2.2 design.
These large innovative XLPE tanks are designed for exceptional durability, reliable performance, and an extended lifespan across a variety of applications. To enhance protection and prolong service life in oxidative environments, such as those involving sodium hypochlorite, they can be manufactured with our industry-leading OR-1000 engineered resin system, known for its remarkable resistance to oxidative chemicals.
These tanks represent the best engineering and design in the tank manufacturing industry, and they are covered under PPC’s industry-leading warranty.
At Poly Processing, we’re focused on delivering high-quality, forward-thinking solutions to meet the evolving demands of the chemical storage industry.
- May 12, 2025
- Topics: Tank Design and Materials, FAQs
About Poly Processing
Posts By Topic
Tech Talk Podcast Episodes
Subscribe By Email
Recent Posts
- Join Us at WEFTEC 2025 Conference & Exhibition
- Effective Wastewater Treatment Chemical Storage
- How to Safely Store Sulfuric Acid to Overcome its Corrosive Nature
- The Complete Journey of Owning and Retiring a Polyethylene Storage Tank
- Is Polyethylene a Storage Solution for Elevated Temperature Tanks?
Tank Configurator
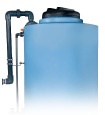
Find the recommended tank and system components for your chemical storage challenge.
Configure a Tank Package