Phosphoric Acid: Storage Solutions During The Water Purification Process
Phosphoric acid is one of the top ten chemicals used in the United States. Phosphates have many uses in the treatment of drinking water. Food grade phosphoric acid is common in the food industry, and it’s even used in pharmaceuticals, detergents, and textile pigments.
Because of its ubiquity and its corrosive qualities, this is an acid that must be handled properly. Any chemical storage solution that contains phosphoric acid must be specifically engineered to handle the chemical properties of this substance.
Let’s look at the use of phosphoric acid in water treatment and the challenges of storing this chemical.
Uses of Phosphoric Acid in Water Treatment
Water treatment plants use phosphoric acid to prevent the after effects of groundwater exposure to iron and manganese, better known as "red water" (from iron) and "black water" (from manganese). When iron and manganese are exposed to air, they oxidize and discolor the water. This creates rust stains from the iron, or brownish-black stains from the manganese. You can sometimes find these stains around bathtub drains or in the laundry.
Often, water treatment facilities use phosphoric acid to prevent or reduce scale formation (from minerals depositing) and corrosion (from low pH and/or dissimilar metals) in the water distribution system.
The chemical can also help reduce soluble lead and copper in tap water. Leaching of pipes and plumbing fixtures results in deposits of lead and copper in drinking water, and phosphates significantly reduce the presence of lead and copper.
Phosphoric Acid Storage Challenges and Solutions
Phosphoric acid is highly corrosive and can form hazardous decomposition products. Contact with certain metals can produce flammable hydrogen gas.
Proper handling isn’t just a best practice — it’s essential to the health and safety of your personnel. Always avoid skin contact and eye contact. Store phosphoric acid in a ventilated area and ensure that personnel are wearing personal protective equipment, including face shields.
Phosphoric acid is delivered at elevated temperatures to keep the chemicals from separating. This causes expansion and contraction stress on the storage tank due to temperature variations. A robust, high density cross linked polyethylene (XLPE) storage tank is required to handle this kind of tank stress.
Crosslinking is simply the formation of bonds between the polymer chains. These bonds are equal in strength and stability to the principal bonds along the polymer backbone. They tie the polymers together, dramatically increasing molecular weight. In fact, the length of the polymer chains and, therefore, the physical properties, is much better than can ever be achieved without crosslinking.
The result is a plastic that possesses impact resistance, tensile strength, and resistance to fracture that linear polyethylene just can’t match. These qualities make cross-linked polyethylene an excellent choice when tank integrity is critical. The structural integrity, heat resistance, and useful life in most cases are unparalleled.
Since phosphoric acid has a tendency to separate, sludge builds up at the bottom of the storage tank. Poly Processing’s IMFO® system provides full tank discharge and one-piece construction using high-density cross-linked polyethylene. This gives you the benefit of easy and safe tank cleaning, as well as the robust tank material required to handle phosphoric acid.
Strength and Durability: Linear Vs. Cross-Linked Polyethylene
Both polyethylene resins are rotational molding-grade resins that have been ground into a powder to allow the material to melt easily during the molding process. Both resins are available in standard colors as well as some custom colors. Both resins are corrosion-resistant polyethylene.
However, the differences are critical. Compared to linear polyethylene, XLPE provides:
- 10 - 20 times the environmental stress crack resistance
- 10 times the molecular weight
- 3-5 times the impact and tensile strength
The four most important factors of high-density linear tanks and cross-linked tanks include:
- Environmental stress crack resistance/notch sensitivity
- Long-term hydrostatic strength
- Toughness and Durability
- Useful Life
In all four of these areas, factual testing and measurements show cross-linked resins are more durable than linear resins.
What About Stainless Steel Tanks for Phosphoric Acid?
Many facilities choose to store phosphoric acid in stainless steel chemical storage tanks. On one hand, steel tanks provide several benefits:
- Steel side walls are resistant to corrosion.
- Steel tanks can be stored indoors or outdoors.
- Steel tanks are easy to regulate temperature.
On the other hand, steel tanks cost three to four times as much as needed. Cross-linked polyethylene tanks provide the same benefits and reliability as steel tanks.
In addition, Poly Processing’s SAFE-Tank® system provides the same double-wall tank system and resistance to corrosion as stainless steel, while offering benefits that steel tanks can’t match:
- Smaller footprint—our double-wall system eliminates the need for a large concrete berm.
- Lower initial costs—XLPE tanks are a fraction of the cost of steel.
- Lower long-term costs—no concrete berm means less maintenance or repair over the life of your storage system.
- Conservation of lost chemical—if a leak occurs, the double-wall system contains any leaked chemical, preventing loss.
When you consider the fact that cross-linked chemical tanks match or exceed the performance of steel tanks — with a 75 percent cost savings — it’s easy to see why our customers prefer Poly Processing’s XLPE chemical storage solutions.
For additional information on how to store Phosphoric Acid, please contact a chemical storage tank expert at Poly Processing.
- December 5, 2022
- Topics: Chemicals
About Poly Processing
Posts By Topic
Tech Talk Podcast Episodes
Subscribe By Email
Recent Posts
- Join Us at WEFTEC 2025 Conference & Exhibition
- Effective Wastewater Treatment Chemical Storage
- How to Safely Store Sulfuric Acid to Overcome its Corrosive Nature
- The Complete Journey of Owning and Retiring a Polyethylene Storage Tank
- Is Polyethylene a Storage Solution for Elevated Temperature Tanks?
Tank Configurator
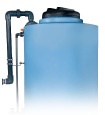
Find the recommended tank and system components for your chemical storage challenge.
Configure a Tank Package