Can Your Storage System Meet the Challenges of Polymers?
Polymers are important chemicals used in the headworks of wastewater treatment plants. They facilitate the flocculation or coagulation of solids in the wastewater to produce large curds of solid materials. They also aid in dewatering of digester cake — reducing the water content to make it easier and less expensive to transport waste materials to the landfill.
Polymers are highly viscous environmental stress cracking agents, which means they present unique storage challenges that require the right storage solution for adequate safety and cost effectiveness. Let’s explore these challenges and solutions.
Polymer Storage Challenges
Cationic and anionic polymers have a high molecular weight. The heavy chemical creates internal pressure and hoop stress, which can cause damage to a storage tank’s wall if your chemical storage tank isn’t properly designed for polymers. Your polymer storage system will require a strong material to withstand the static load pressure on the bottom third of the storage tank.
Because of their high molecular weight, polymers are very slippery. They can pose a safety hazard if your storage tank develops a leak that spills onto the floor or the deck of the walkway.
Polymers can also be a stress cracking agent. The chemicals are manufactured at elevated temperatures and may be delivered to your facility before they have cooled all the way down. The heat can compromise the strength of the tank wall, significantly reducing the useful life of your polymer storage system and creating an opportunity for cracks and leaks.
Polymers can be delivered “neat,” or concentrated, but they may require blending. If so, your chemical storage tank will need to be designed and engineered to meet the unique challenges that blending introduces.
Polymer Storage Tips
Because polymers present unique challenges, it’s crucial to design a storage system that will perform reliably for years. Be sure your storage solution meets the following standards.
-
Superior tank strength. High-density cross-linked polyethylene (XLPE) offers superior strength at a long-term cost advantage for storing heavy polymers. Poly Processing’s XLPE tanks often provide 15-20 years of service in this application.
-
Leak prevention.To reduce the potential for leaks and spills, and to minimize slips and falls, it’s important not to penetrate the sidewall of the tank. Poly Processing’s Slope-Bottom IMFO® System molds the flange into the bottom of the tank during production. There are no sidewall fittings to introduce additional potential for leaks. Since the flange is created from the same material as the tank – it’s not a metallic insert introduced during or after production – the IMFO System provides superior tank strength for storing heavy weight polymers.
-
Easy blending. Open top tanks are available in a variety of sizes. Tanks can be highly customized to accommodate a mixer in your operation.
-
Minimal corrosion. As opposed to steel or fiberglass, Poly Processing cross-linked polyethylene tanks offer a cost effective, durable, high-strength storage solution that resists corrosion.
Store Your Polymers Properly
Polymer chemicals present unique challenges that require specialized storage solutions. Be certain that your storage system is properly designed and built to meet these challenges. Poly Processing has over 40 years of experience storing polymers — we can help engineer the safe and effective system you need.
Download our Polymers Storage Guide for more details on properly storing polymer or contact a chemical storage tank expert today to discuss a plan for safe polymer storage.
- February 17, 2020
- Topics: Chemicals
About Poly Processing
Posts By Topic
Tech Talk Podcast Episodes
Subscribe By Email
Recent Posts
Tank Configurator
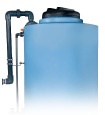
Find the recommended tank and system components for your chemical storage challenge.
Configure a Tank Package