How Much Pressure Is Too Much for a Polyethylene Storage Tank?
When you design a chemical storage tank system, you have to consider the factors that impact the tank’s service life. Not only do you have to make sure that the tank material and fitting materials are compatible with the chemical you’re storing, it’s also important to consider the functionality of the tank — for example, how it responds to pressure.
You need to know exactly how much pressure your chemical storage tank can safely handle. This is an issue for every chemical tank, no matter what material it’s made of. Fortunately, cross-linked polyethylene storage tanks have remarkable durability compared to many other materials. That said, you need to know your tank’s pressure limits.
Pressurization in Polyethylene Tanks
Cross-linked polyethylene (XLPE) tanks are robust, because the molecular bond gives the tank better mechanical properties than high-density polyethylene tanks provide.
Poly Processing performed a test to failure with XLPE vs HDPE. This test was designed to show the difference in failures between XLPE and HDPE and does not relate to "working" pressure.
We pressurized both tanks using a 5.5 horsepower water pump and a fire hose to fill the tanks with water to the point of failure. The linear polyethylene tank catastrophically failed at 9 psi of water pressure.
The cross-linked tank failed at 10 psi, but did not fail catastrophically. The tank developed a 6-8" crack at the top of the tank but did not completely break apart. The cross-linked polymer chains around the crack site held the tank together.
Watch the video below to see the pressure test for yourself.
If this had been a real-world scenario, less product would have been lost and the leak would have posed less of a hazard to people, equipment, and the environment. This test is a testament to the robustness of cross-linked polyethylene and its ability to withstand even the harshest environments.
The test is also a good indicator of what might happen as a tank's integrity is compromised over time by chemical attack or UV degradation. It's important to regularly inspect your chemical tanks to determine their longevity.
Pressurization and Vacuum Affect Service Life
Pressure and vacuum are leading reasons why a chemical storage tank may have a shorter service life than expected. Vacuum is the opposite of positive pressure, but it plays a role in the wear and tear on a polyethylene tank. If a tank is sealed and chemical is discharged, the tank could collapse if proper venting is not in place.
Conversely, if too much air builds up in the tank, especially during pneumatic fill, the plastic tank wall is placed under heavy stress and can fail. It’s important to ensure there is only atmospheric pressure, without vacuum or positive pressure, to store your chemicals safely and to maximize the storage tank’s service life.
Chemicals and Tank Pressurization
Many static chemicals will build pressure, given time. There are certain chemicals that fume more than others, and that fuming creates greater pressure on the tank. Hydrochloric acid, acetic acid, and ammonias are highly fuming chemicals that should be stored with a scrubber system that treats and safely discharges the chemical fumes.
It’s important to make sure the scrubber system does not create more back pressure in the tank than 6 inches of water column. Use a scrubber system with proper pipe sizes and adequate plenum holes or slots to avoid over-pressurization of the tank. Poly Processing can match a specific scrubber system to your particular tank.
Other ways to ensure that your chemical storage tank does not become over-pressurized include:
- Choosing the right manway cover
- Making sure the materials in your tank system are compatible with the chemical application
- Ensuring all fittings and accessories are properly connected
Talk to a chemical storage expert for design recommendations on your specific chemical tank application.
- January 27, 2020
- Topics: Fittings and Accessories
About Poly Processing
Posts By Topic
Tech Talk Podcast Episodes
Subscribe By Email
Recent Posts
- Join Us at WEFTEC 2025 Conference & Exhibition
- Effective Wastewater Treatment Chemical Storage
- How to Safely Store Sulfuric Acid to Overcome its Corrosive Nature
- The Complete Journey of Owning and Retiring a Polyethylene Storage Tank
- Is Polyethylene a Storage Solution for Elevated Temperature Tanks?
Tank Configurator
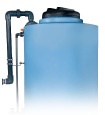
Find the recommended tank and system components for your chemical storage challenge.
Configure a Tank Package