Crosslinked Polyethylene Vs. Fiberglass Reinforced Plastic Tanks
Purchasing a high-performance chemical storage tank is a significant investment for your company, and choosing the right tank for your needs isn’t always an easy decision. If you’re deciding between a fiberglass reinforced plastic (FRP) tank and crosslinked polyethylene (XLPE) tank, be sure you understand the differences between them and know what to expect in terms of cost, maintenance, service, delivery times, and protection.
FRP tanks are coated with an interior chemical resin. Their structural layer is composed of chopped glass fiber or filament-wound fibers and resin. XLPE is a thermoset resin specifically engineered for critical applications like chemical storage.
Let’s explore seven important benefits of XLPE over FRP chemical tank systems. Evaluate these benefits thoughtfully as you select your next chemical storage tank system.
XLPE Offers Seamless Construction for Greater Strength
Fiberglass Reinforced Plastic tanks are filament-wound or hand laid up. Fibers are intertwined into a nexus veil that is wound onto a spool. In this spool, the fibers create a fiberglass layer with added resin, which keeps them bound together. Fiberglass tanks are constructed with seams (due to the winding).
This method of manufacturing inherently creates the opportunity for weak points that are vulnerable to leaks. In addition, FRP tank manufacturers add the top and bottom of the tank post-production, further increasing the risk of leaks.
Conversely, crosslinked polyethylene tanks are rotationally molded, producing a one-piece construction with no vulnerable seams. As opposed to fiberglass tanks, rotationally molded tanks are a homogenous, one-layer construction. This one layer construction eliminates potential weak spots in the tank structure and eliminates wicking or delamination that can occur from chemical attack or poor construction.
Chemical Wicking into the Tank’s Walls
Because of the structure of fiberglass, harsh chemicals can wick into fiberglass tank walls over time, compromising the tank life. Eventually, the chemical resin barrier on the interior wall can be compromised, and the chemical can make its way into the structural area of the tank. This structural area usually isn’t designed to provide the chemical compatibility that the interior resin provides. As a result, the fibers can begin to break down, and eventually, the tank fails.
While there are repairs that you can sometimes make, they’re usually only temporary. Eventually you will need to replace your fiberglass tank.
That’s one of the reasons that most fiberglass tanks don’t have the same warranty Poly Processing provides for our corrosion resistant tanks. Even the harshest chemicals can’t seep into high-density crosslinked polyethylene tank walls.
Cost of Tank Ownership
Fiberglass tanks are more costly than crosslinked polyethylene tanks, sometimes three to five times more. Delivery times can be three to four times longer as well. FRP storage tanks have a higher upfront cost in general, and the lifetime cost of ownership is higher. FRP tanks require more maintenance than crosslinked polyethylene tanks, costing you time, resources and money.
Because FRP tanks are painted or have a gel coat on the outside of the tanks, they need to be recoated on occasion. This is especially true for outdoor tanks because the fiberglass requires UV protection to prevent additional wear. XLPE tanks never need to be painted or coated, because the entire wall has UV additives throughout the tank.
Special Handling Considerations
Fiberglass tanks are inflexible, which makes them vulnerable to cracking. Extreme care must be taken anytime you move an FRP tank, especially during installation. As a result, these tanks often sit on a special wicking mat so that any leaks in the bottom of the tank can be easily seen as the chemical spreads throughout the mat.
Crosslinked polyethylene tanks are much more durable, and can easily be moved at any time. In fact, our durability testing drops filled tanks from as high as 45 feet above the ground—without splitting or leak leaking.
Molded Tank Fittings vs. Traditional Attachments
All FRP fittings are added onto the tank after production, which creates the opportunity for leaks at the attachment point. Poly Processing’s IMFO® (Integrally Molded Flanged Outlet®) fitting prevents this problem because the fitting is integrally molded into the tank itself. It’s not an attachment, but a single part of the chemical tank. This innovation removes potential stress points and allows no opportunities for leaks.
NSF/ANSI 61 System Certification
Poly Processing is committed to ensuring that our polyethylene chemical storage systems meet industry standards and are NSF/ANSI 61 certified. In fact, among chemical storage tank manufacturers, Poly Processing is the only one with a complete chemical storage tank system that is NSF/ANSI-61 certified. Currently, we have NSF 61 Certification for 38 of the most popular water treatment chemicals on our XLPE tank systems. Additionally, our certifications cover XLPE tanks with the OR-1000® System.
Most FRP tanks hold the basic NSF/ANSI 61 certification for only one specific application, potable water.
Delivery Lead Times
We know that delivery times are critical to our customers. That's why we work diligently to ship every order within 8-12 weeks. Most FRP tank manufacturers and poly tank manufacturers are giving their customers a 24-40 week shipping window based on lack of raw material sourcing, Covid-19, etc. At Poly Processing Company, we can deliver your product in one third of that time.
Before you order an FRP tank, make sure the manufacturer gives you the price and the lead time up front. Otherwise you could be in for a rude awakening.
Trusted, consistent, and expeditious, Poly Processing’s rotationally molded crosslinked tanks are by far the toughest polyethylene tanks offered to the chemical market. With our 6-8 week delivery window, we strive to deliver peace of mind and an ease of business to each and every customer.
Learn more about FRP, XLPE and the wide range of other tank options in our tank buying guide.
- March 18, 2024
- Topics: Value Added
About Poly Processing
Posts By Topic
Tech Talk Podcast Episodes
Subscribe By Email
Recent Posts
- The Largest Crosslinked True Full Discharge Tanks Available: 15,500 IMFO and 15,000 Sloped Bottom IMFO
- Contained Bottom Discharge for Double-Wall Tank
- Join Us at WEFTEC 2025 Conference & Exhibition
- Effective Wastewater Treatment Chemical Storage
- How to Safely Store Sulfuric Acid to Overcome its Corrosive Nature
Tank Configurator
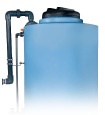
Find the recommended tank and system components for your chemical storage challenge.
Configure a Tank Package