Chemical Storage Lessons From the Roanoke Chemical Spill
Recently, a chemical storage spill occurred at a Roanoke metals processing plant. A forklift punctured a storage tank containing hydrochloric acid. This pungent liquid is a strong, highly corrosive acid that creates toxic and potentially fatal fumes. Because of the high-risk chemical involved, the plant was quickly evacuated. Thankfully, the spill was less than 100 gallons and could be contained with minimal impact on the plant production schedule, and most importantly, no one was injured.
While a catastrophe was averted, several lessons about safe chemical storage are found in this incident.
1. The Importance of Using a Puncture Resistant Material
When poly storage tanks are placed in environments where other machines, like forklifts, are operating, there’s an inherent risk involved. In this type of scenario, we recommend a solution capable of withstanding potential damage or punctures. High-density crosslinked polyethylene (XLPE) is our most robust tank material, built to resist punctures from impact and provide superior safety.
In addition to choosing a tank with a proven material, it’s important to know that the tank has been thoroughly tested and proven. Every Poly Processing chemical storage tank is tested to ensure ASTM D 1998 standards are met or exceeded. Our tanks endure multiple tests in order to understand their limits.
2. The Importance of Secondary Containment – Regardless of Space Limitations
In the Roanoke incident, the punctured tank was housed in a specially designed chemical containment room. This setup kept the chemical spill from entering the surrounding environment where it could have potentially damaged critical equipment and put employees at risk.
Of course, not all plants have the space for a fire- and explosive-proof self-contained room. This is certainly an important thing to think about if you are building a plant in the future, but if you already have a solid facility to work with and are tight on space, there are other options available to keep your chemicals, employees, and environment safe.
There are two different types of secondary containment basins: cylindrical and rectangular. These are used for the nesting of traditional vertical or vertical IMFO® tanks to meet secondary containment requirements.
If your plant truly lacks the space for separate containment basins, the SAFE-Tank® is a viable, cost-effective secondary containment option. This storage and containment system offers secondary containment within the tank itself, providing you with solid investment and peace of mind without taking up much additional space.
3. The Importance of Preparation to Prevent Catastrophe
Unfortunately, chemical spills do happen. Thankfully, preparation is the most important step to preventing larger problems. Storing chemicals in a strong, puncture and impact resistant tank, and having effective secondary containment in the event of a spill, helps to prevent a catastrophe.
Learn more about secondary containment options in our comprehensive ebook.
Photo Credit: Artic Warrior via Flickr cc
- August 5, 2014
- Topics: News and Customer Stories
About Poly Processing
Posts By Topic
Tech Talk Podcast Episodes
Subscribe By Email
Recent Posts
- The Largest Crosslinked True Full Discharge Tanks Available: 15,500 IMFO and 15,000 Sloped Bottom IMFO
- Contained Bottom Discharge for Double-Wall Tank
- Join Us at WEFTEC 2025 Conference & Exhibition
- Effective Wastewater Treatment Chemical Storage
- How to Safely Store Sulfuric Acid to Overcome its Corrosive Nature
Tank Configurator
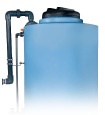
Find the recommended tank and system components for your chemical storage challenge.
Configure a Tank Package