How to Determine the Ideal Tank System for Chemical Storage
In industries where chemical storage is essential, selecting the right tank size and system is critical. An incorrect choice can lead to regulatory penalties, safety hazards, and financial losses.
This article will guide you through the process of determining the ideal tank size for your chemical storage needs, while outlining the considerations for capacity, material, safety, and compliance.
Assess Your Storage Needs
The first step in determining your ideal tank is to start with the chemical being stored. At Poly Processing Company, we look at the chemical being stored first. This will determine what type of tank, what type of material, and what type of accessories will need to be part of the tank system.
Different chemicals exhibit diverse physical and chemical properties, which may impose specific requirements on storage conditions. It's crucial to identify the types of chemicals you'll store—whether they are corrosive, fuming, reactive, etc. This assessment will inform decisions regarding material selection and tank design, as certain chemicals may necessitate specific safeguards or alternatives.
Current and Future Needs
The second step in determining your ideal tank size is to assess your current storage needs along with any future requirements. Calculate the volume of chemicals you currently need to store while considering potential increases due to business growth or seasonal changes.
Understanding current and future demand will help ensure that your tanks are appropriately sized, eliminating the risk of overflow or supply shortages. This is also a good time to think about having a backup chemical storage tank as well, in case of scenarios when business dictates the need for more chemicals.
Regulatory Compliance
Compliance with environmental and safety regulations is paramount when designing a chemical storage tank. Familiarize yourself with the guidelines mandated by agencies such as the Environmental Protection Agency (EPA), National Fire Protection Association (NFPA), Occupational Safety and Health Administration (OSHA), International Building Code (IBC), and other possible local and national regulations.
A well-structured chemical storage plan will not only serve to protect your workspace but also ensure you’re operating within legal parameters.
Safety Considerations
Safety protocols are critical in designing your chemical storage tank. When planning your storage area, include features like secondary containment, proper ventilation, leak detection systems, and appropriate signage.
Your goal should be to create a safe environment that minimizes risk to workers and the surrounding community.
Determine Tank Capacity
The design of your tank significantly influences its volume. Common crosslinked polyethylene geometric forms include double wall tanks, full discharge tanks, vertical tanks, and cone-bottom tanks. Use the Poly Processing website to select the tank design and appropriate volume that is right for you.
Consider Tank Materials
The choice of tank material is of utmost importance. Ensure the material you select is compatible with the chemicals being stored to prevent corrosive damage or dangerous chemical reactions.
Common chemical tank materials include:
- Stainless Steel: Offers good corrosion resistance for various chemical applications but can be very costly.
- Linear Polyethylene (LDPE): A cost-effective option that is versatile across many applications, including smaller agricultural tanks and water tanks.
- Fiberglass: Because fiberglass tanks are constructed by winding, they inherently have seams. This method of manufacturing inherently creates the opportunity for weak points that are vulnerable to leaks. In addition, fiberglass tank manufacturers add the top and bottom of the tank post-production, further increasing the risk of leaks.
- Crosslinked Polyethylene (XLPE): XLPE tanks possess excellent impact resistance, tensile strength, and resistance to fracture that linear polyethylene just can’t match. These qualities make cross-linked polyethylene an excellent choice when tank integrity is critical. The structural integrity, heat resistance, chemical resistivity, and useful life in most cases are unparalleled.
The Importance of Secondary Containment
In today’s world, where environmental concerns are on the rise, industries handling or storing chemicals or hazardous materials must implement robust safety measures to prevent spills and leaks. One essential aspect of this safety protocol is establishing a secondary containment system.
A secondary containment system is vital to mitigate spill risks. This containment can take the form of dikes, berms, or engineered double wall tanks or SAFE-Tanks® designed to hold any potential leaks from your tanks.
Capacity
There are several ways to achieve secondary containment. Often, facilities construct a dike or berm around their storage tank areas. Poly Processing recommends using an engineered double wall tank, also known as the SAFE-Tank.
The SAFE-Tank system has several benefits over a dike or berm. Your SAFE-Tank will:
- Provide 110% secondary containment using the same material as the primary tank.
- Equalize the liquid and allow the chemical to be continually used until it is convenient to repair the tank if needed.
- Be ideal for chemicals like sulfuric acid that can have dangerous exothermic reactions to water.
- Eliminate the expense and maintenance of secondary concrete containment.
- Minimize the system’s footprint by providing secondary containment in a more compact way.
Adding a bellows transition fitting maximizes your SAFE-Tank® system’s safety and performance.
The capacity of your secondary containment system is crucial in guaranteeing that it can handle any potential leaks. The general guideline is that the secondary containment should be sized to hold at least 110% of the largest tank's capacity.
This sizing ensures that even in the event of a significant leak, there will be enough containment to prevent the hazardous materials from reaching the environment, thus safeguarding water sources and local ecosystems.
The materials used for constructing the secondary containment system play a vital role in its efficacy. It is essential to use impervious materials that are capable of resisting the chemicals contained within the tank. That’s why a Poly Processing SAFE-Tank using crosslinked polyethylene is an excellent choice — both the containment tank and the primary tank are manufactured using crosslinked polyethylene, which stands up to even the most aggressive chemicals.
When selecting materials, consider the nature of the stored substances, as some chemicals may require specialized containment solutions to avoid reactions or degradation of materials.
Other Factors to Consider
Space Constraints
Before installing your tank and secondary containment, assess the available space to ensure the tank will fit comfortably in the designated area. It is vital to allow for adequate access and ventilation around the tank and containment system to facilitate safe operation and maintenance.
Installation Environment
The location of the containment system significantly affects its design and implementation. Determine whether the tank will be installed indoors, outdoors, above ground, or underground, as each environment will have different requirements for construction and maintenance.
Future Expansion
Looking ahead, consider potential growth and expansion needs. Choose tank sizes and designs that accommodate future increases in production or storage capacity or that can be economically replaced with larger capacity tanks. This foresight can save considerable costs down the line and minimize disruptions during installations.
Ready to Get Started on Your Tank Design?
Contact a chemical storage tank expert today to see how we can help you design the right drawings for your specific storage needs.
Industry News
For over five decades, Poly Processing has been at the forefront of innovation in chemical storage tank design and manufacturing. Reinforcing our commitment to advancing crosslinked polyethylene (XLPE) tank technology, we are thrilled to unveil our latest update to our storage tank solutions: the 15,500-gallon IMFO tank, the 15,000-gallon Sloped Bottom IMFO tank, and the 15,500-gallon Vertical tank, are all available in specific gravities up to 2.2 design.
These large innovative XLPE tanks are designed for exceptional durability, reliable performance, and an extended lifespan across a variety of applications. To enhance protection and prolong service life in oxidative environments, such as those involving sodium hypochlorite, they can be manufactured with our industry-leading OR-1000 engineered resin system, known for its remarkable resistance to oxidative chemicals.
These tanks represent the best engineering and design in the tank manufacturing industry, and they are covered under PPC’s industry-leading warranty.
At Poly Processing, we’re focused on delivering high-quality, forward-thinking solutions to meet the evolving demands of the chemical storage industry.
- May 5, 2025
- Topics: Value Added
About Poly Processing
Posts By Topic
Tech Talk Podcast Episodes
Subscribe By Email
Recent Posts
- Join Us at WEFTEC 2025 Conference & Exhibition
- Effective Wastewater Treatment Chemical Storage
- How to Safely Store Sulfuric Acid to Overcome its Corrosive Nature
- The Complete Journey of Owning and Retiring a Polyethylene Storage Tank
- Is Polyethylene a Storage Solution for Elevated Temperature Tanks?
Tank Configurator
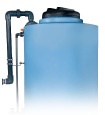
Find the recommended tank and system components for your chemical storage challenge.
Configure a Tank Package